Pipe End Plugs
The safe, fast and efficient method of installing temporary test caps
Pipe End Plugs reduce time and material costs, minimise environmental impact and improve testing productivity.
STATS' range of Pipe End Plugs cover two separate products with the I-PEP™ fitting the pipe internally and the patented E-PEP™ gripping the pipe externally.
3/4" - 42" size range
350 Bar/5076 PSI Pressure Limit
hydraulic above 2" activitation
AMSE B31.3 testing ability
ASME B36.10/B36.19 Interchangeable Seals
Pipe End Plugs are typically used during the construction and fabrication of pipe spools and piping systems. These fail-safe tools cap open-ended pipe, facilitating hydrostatic leak, reinstatement pressure and strength tests.
Our Pipe End Plugs are quick and easy to install, are hydraulically activated and provide a safe and cost-effective solution for pipe capping.
Key Takeaways
- A fast and efficient method of installing temporary test caps on plain end pipe
- Use as a mechanical end/test cap instead of welding sacrificial end caps
- Two separate products with the I-PEP™ fitting the pipe internally and the patented E-PEP™ gripping the pipe externally
- I-PEP above 24" - Hydrostatic leak and strength tests up to 229 bar / 3321 psi
- E-PEP up to 24" Hydrostatic leak and strength tests up to 350 bar / 5076 psi
- Reduces time and material costs
- Requires minimal preparation or post-test work on pipes, improving test productivity
- For use in planned shutdowns or emergency repair work
- Sale or rental options available, complete with full ancillary equipment
- Available as a product or as part of a service
- Fail-safe design
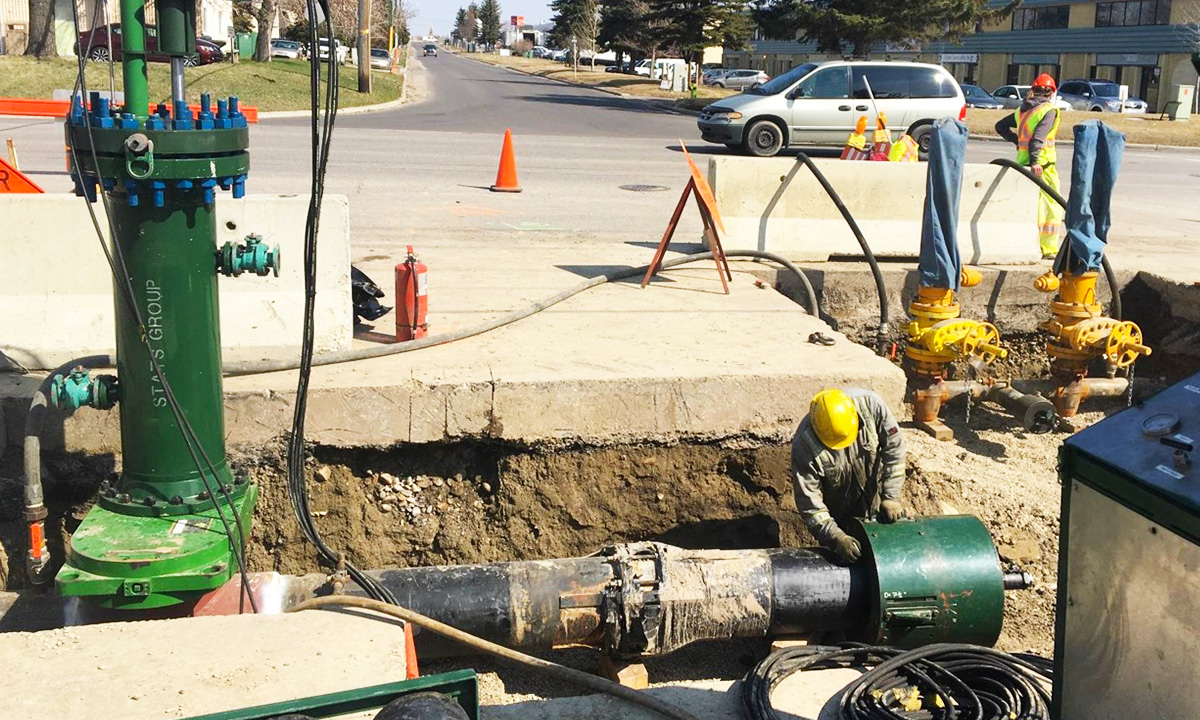
Case Study - Pipe End Plugs facilitate Pipe Spooling for Aasta Hansteen Field
Testing 17 km of BuBi® mechanically clad flowlines being reeled onto the vessel and installed at the Aasta Hansteen gas field.
Video - Hydrostatic Test Utilising the External Pipe End Plug (E-PEP™)
This 2 minute video demonstrates the use of STATS External - Pipe End Plug (E-PEP) during hydrostatic testing.
E-PEP™ – External Pipe End Plugs: These plugs are fitted to the pipe end and actuated hydraulically, gripping the pipe externally. The hydraulic pressure activates a mechanical lock assembly that grips the pipe's outside diameter and simultaneously energises an elastomeric seal within the internal diameter. E-PEPs cover pipe sizes from 3” to 24”.
I-PEP™ – Internal Pipe End Plugs: These plugs are inserted into the bore of the pipe and actuated hydraulically, gripping the pipe internally. Similar to E-PEPs, hydraulic set pressure activates a mechanical lock assembly gripping the internal diameter and energising an elastomeric seal. Hydraulic I-PEPs cover sizes from ¾” to 42”, while mechanical tools are used for sizes ¾” to 2” and are fitted with securing clamps.
Pipe End Plugs function through hydraulic actuation which engages a mechanical lock assembly, providing grip either on the outer (E-PEP) or inner (I-PEP) diameter of the pipe. This action also simultaneously energises an elastomeric seal.
They include a through-port, enabling the system to be filled, pressurised, or vented directly through the plug. Hydraulic activation is used for sizes above 2 inches. The internal/external grip lock assembly applies even, linear and circumferential grip load around the host pipe, eliminating localised material deformity and localised stress fractures.
These tools are designed to be robust enough for the demands of the fabrication yard environment. They provide significant operator benefits, including reduced cost and time compared to traditional methods like welding and cutting end caps. They are described as simple, straightforward to install, taking only minutes to set and activate.
A Mechanical Alternative to Sacrificial End Caps
To accelerate project timelines and eliminate the need for welding, we also offer our Pipe End Plugs as a mechanical alternative to sacrificial end caps for containment.
It's a practical, mechanical solution to welding dome end caps for line stop deployment activities. The E-PEP Mechanical End Cap is a faster alternative, eliminating the subsequent step of welding and cutting off welded caps on completion of works.
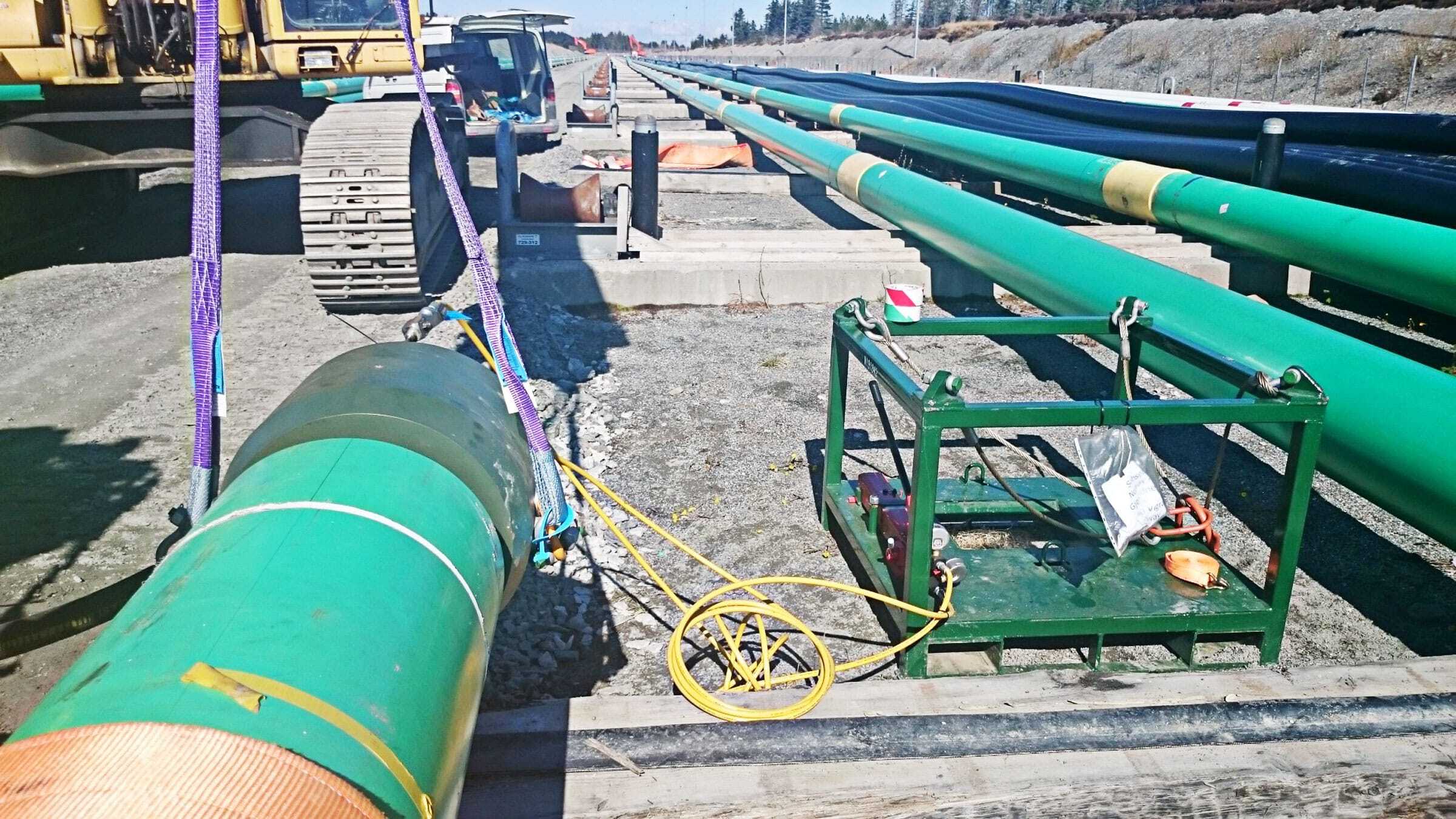
Field Proven PIPE END PLUG TECHNOLOGY
A key feature of their safety and operation is the fail-safe design. The test pressure across the tool creates a differential pressure that self-energises the locks and seals, maintaining the isolation securely. This means the isolation is maintained even if the hydraulic control system is compromised. To remove the plug, hydraulic pressure is applied to the unset circuit, retracting the lock assembly and de-energising the seal.
Our Pipe End Plugs handle pressure testing differently to other test plugs, removing local stress issues if testing is near yield.
STATS' Pipe End Plugs are non-destructive, ensuring no damage to the interior or exterior walls of the pipes or vessels. They are designed with generous radial clearance to accommodate typical internal obstructions like weld beads or ovality. High-performance elastomeric seals provide a leak-tight seal. The grip load applied by the lock assembly is even and circumferential, preventing localised deformity or stress fractures in the pipe. They can be used in horizontal, vertical, and inclined piping.
The design allows for quick and efficient pressure testing with minimal pipe end preparation and no remedial work required after removal. They are designed in accordance with STATS engineering standards, which are based on international codes such as ASME B31.3, and their sizes align with ASME B36.10 and ASME B36.19 schedules. The pressure rating can be up to 350 bar / 5076 psi for E-PEPs and 229 bar / 3321 psi for I-PEPs, however higher pressure are available on request.
While primarily designed for construction and pressure testing, Pipe End Plugs, like other isolation plugs, can also be used as subsea abandonment tools. In this role, they are used to cap open pipe ends.
A key difference between our end plugs and other test plugs is how they handle pressure testing. While conducting high pressure testing which could cause local stress issues if testing near yield, Pipe End Plugs address this by placing the locks on the outside (E-PEP) and the seal on the inside to squeeze the pipe instead of causing hoop stress.
For larger internal plugs (I-PEPs), a special test plug module using an annular test tool type piston can be used to avoid over-stressing the pipe during high-pressure testing.
This technology can be procured as a product or as part of a service, such as isolation or emergency repair service, and is available to be bought as a back-up product. Thanks to our extensive global manufacturing base, we can usually deploy them within 24 to 48 hours.
FIELD PROVEN
E-PEP™ – External Pipe End Plugs
The E-PEP series of patented Pipe End Plugs are fitted to the pipe end and hydraulically actuated, gripping the pipe externally.
Features, Codes and Standards
- All Pipe End Plugs are designed to STATS engineering standards (based on international codes)
- This facilitates testing in accordance with ASME B31.3 and similar piping codes
- Sizes are based on standard pipe with interchangeable seals to cover ASME B36.10 and ASME B36.19 schedules
- E-PEP covers pipes from 3" to 24"
- Fail-safe design
- Pipe End Plug through-port system allows filling / pressurisation and venting of test medium
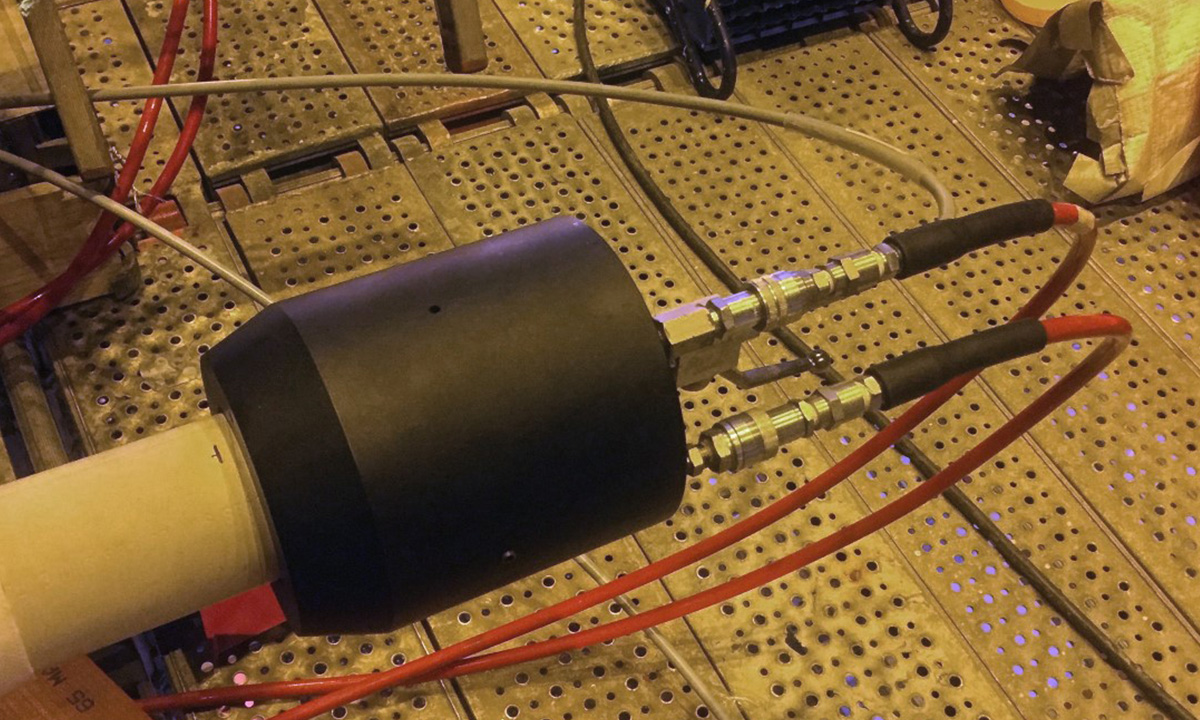
The introduction of hydraulic set pressure activates a mechanical lock assembly that grips the outside diameter of the pipe whilst simultaneously energising an elastomeric seal in the internal diameter.
This allows the pipework to be quickly and efficiently pressure tested with minimum preparation to the pipe end and no remedial work after the E-PEP is removed.
A through-port allows the system to be filled and pressurised or vented through the E-PEP.
All Pipe End Plugs are designed in accordance with STATS engineering standards (based on international codes) to facilitate testing in accordance with ASME B31.3 and similar piping codes.
Sizes are based on standard pipe with interchangeable seals to cover ASME B36.10 and ASME B36.19 schedules.
FIELD PROVEN
I-PEP™ – Internal Pipe End Plugs
The I-PEP series of Pipe End Plugs are inserted into the bore of the pipe and hydraulically actuated. These tools internally grip the pipe allowing hydrostatic pressure tests to be quickly and efficiently performed. The introduction of hydraulic set pressure activates a mechanical lock assembly that grips the internal diameter of the pipe whilst simultaneously energising an elastomeric seal.
Features, Codes and Standards
- All Pipe End Plugs are designed to STATS engineering standards (based on international codes)
- This facilitates testing in accordance with ASME B31.3 and similar piping codes
- Sizes are based on standard pipe with interchangeable seals to cover ASME B36.10 and ASME B36.19 schedules
- Pipe sizes from ¾” to 42”
- For sizes ¾” to 2” mechanical tools are used and fitted with securing clamps for added safety
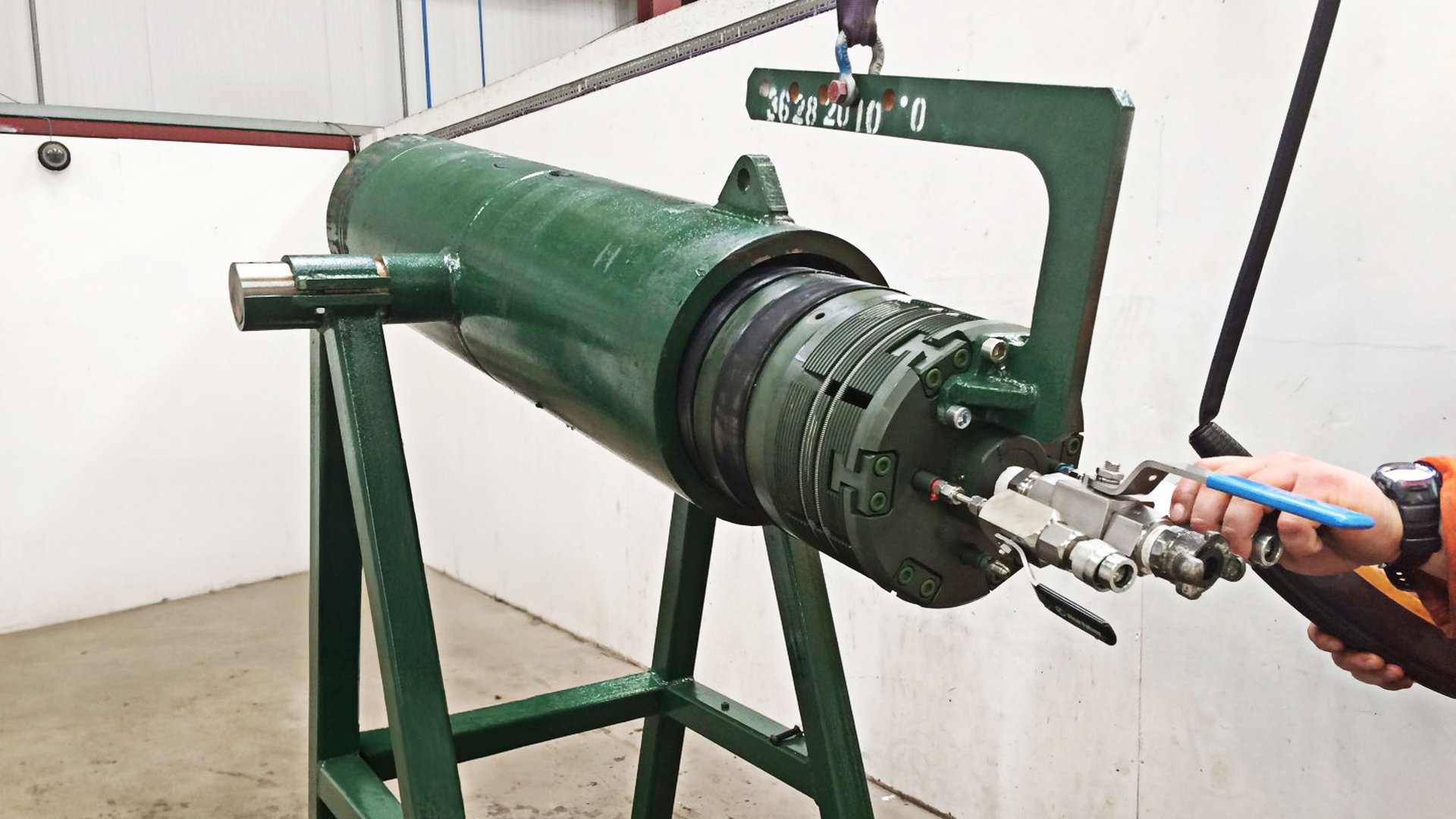
12" I-PEP™
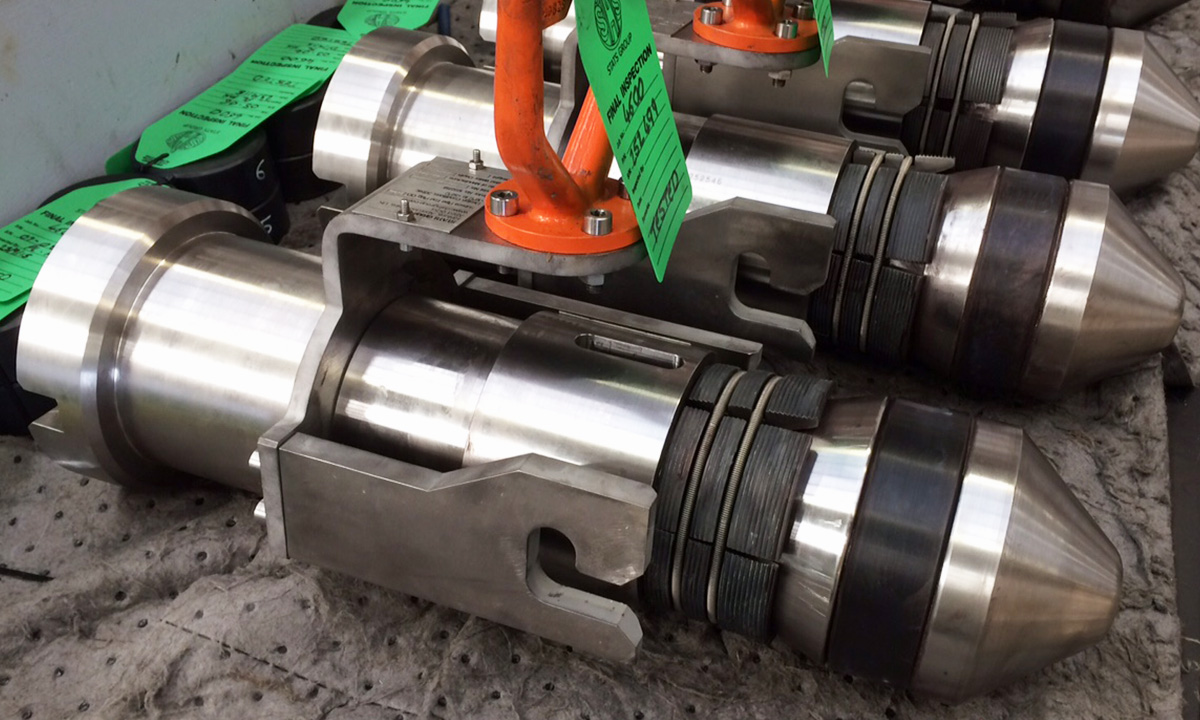
This allows the pipework to be quickly and efficiently pressure tested with minimum preparation required to the internal surface of the pipe and no remedial work after the I-PEP is removed. A through-port allows the system to be filled and pressurised or vented through the I-PEP. To remove the I-PEP from the pipe, hydraulic pressure is applied to the unset circuit, retracting the lock assembly and de-energising the seal allowing the tool to be removed.
Hydraulic I-PEPs cover pipe sizes from ¾” to 42”, however for sizes ¾” to 2” mechanical tools are used and fitted with securing clamps for added safety.
Subsea Pipeline Plugging & Abandonment
For subsea abandonment, Pipe End Plugs can be operated by ROV. Despite being relatively simple tools, their installation in a subsea abandonment context carries risks, particularly the danger to divers from pressure fluctuations and the potential for flow into the pipe bore which could suck a diver inside.
Special requirements from clients, such as dewatering ports or designing them to double as lift and pull tools, can often be accommodated.

Local Everywhere
Instead of flying people and equipment all over the world, we've set up fully-functional bases in nine strategic locations. These bases enable us to employ local technicians, work with local manufacturers, and invest in local economies. They're a significant investment, but our regional bases are key to delivering the best possible service for our clients - and minimising the environmental impact of our work.
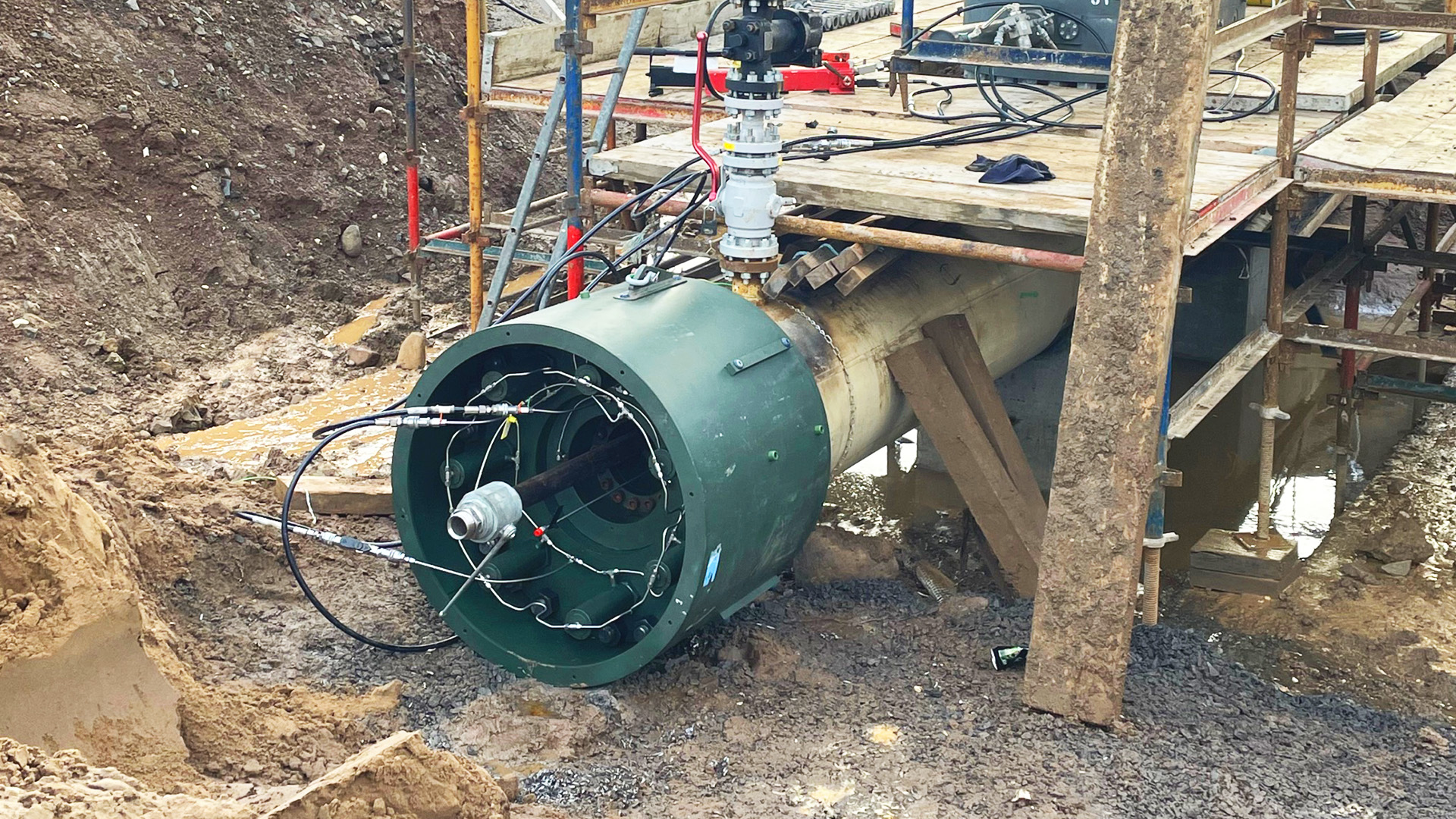