Case Study
10” BISEP | Brent Bravo & Delta Platforms, North Sea, UK
Tool - BISEP Plugging Tool, Tecno Plug Isolation Tool, Mechanical Pipe Connector, Hot Tap Clamp
Location - North Sea
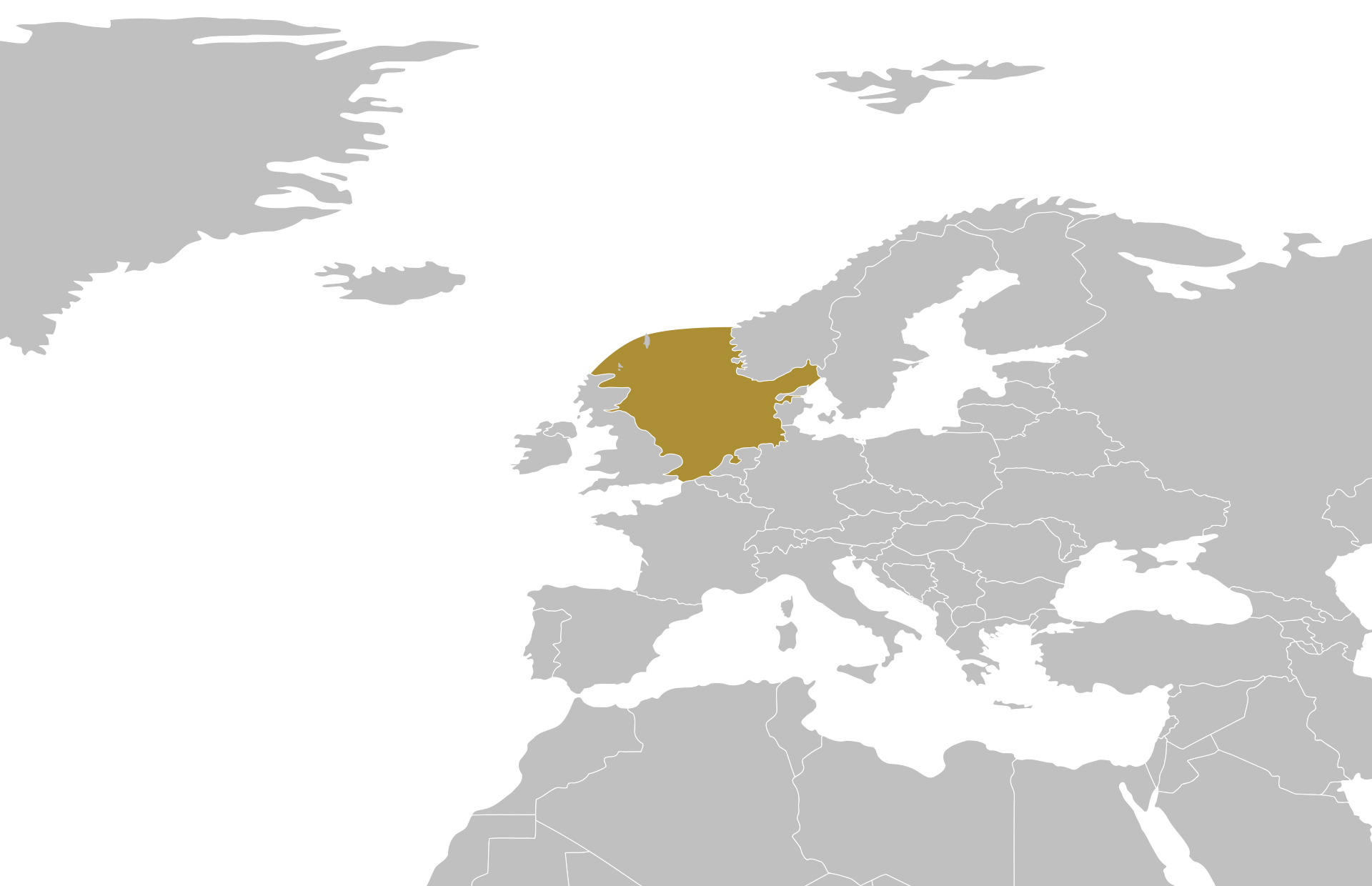
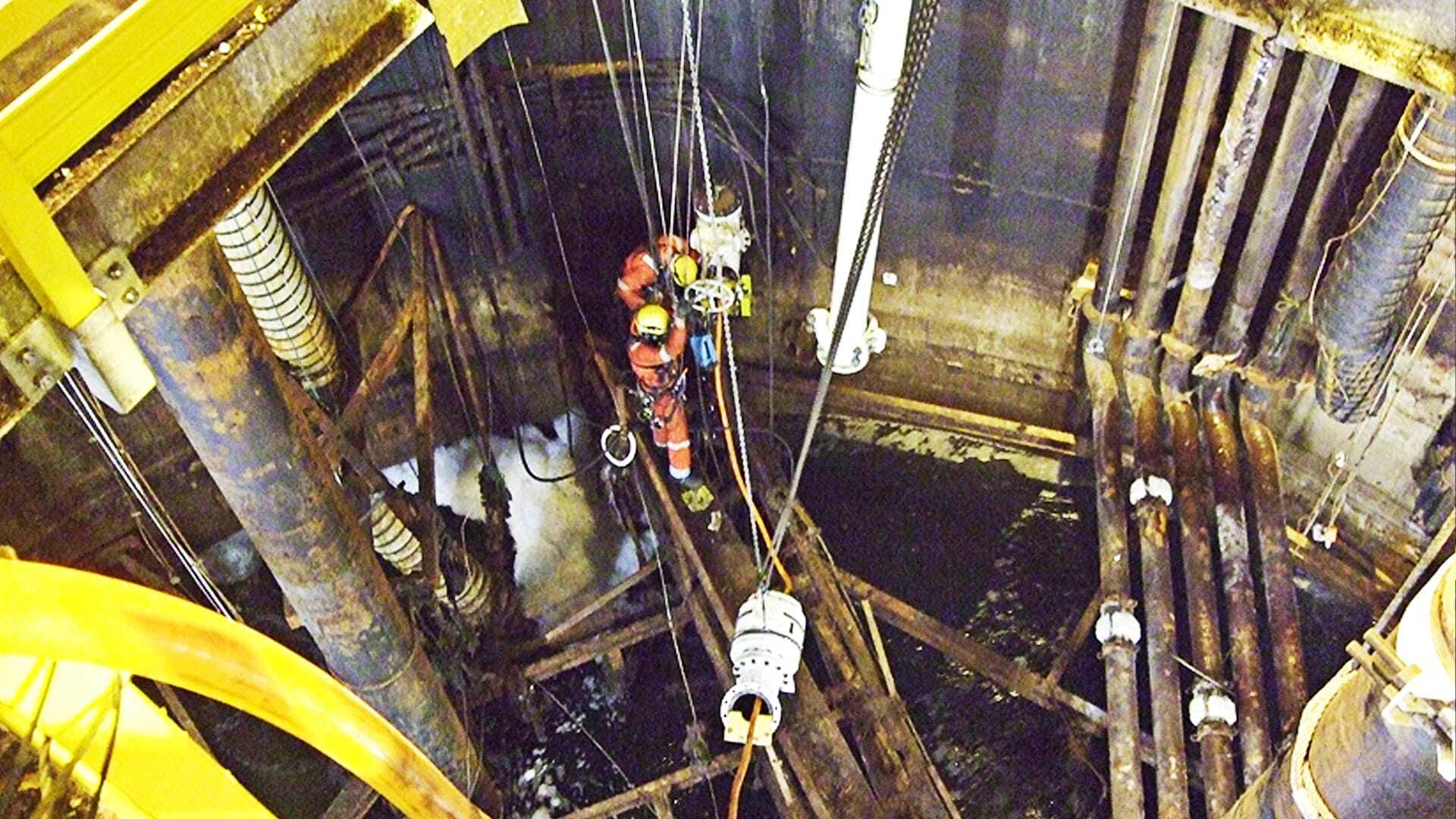
Innovative, ground breaking and even, on occasion, not possible, just a few of the references to the successfully completed Brent Bravo and Brent Delta Cell Fill Line Replacement Project. Early in 2005, STATS were awarded the contract by Shell / Sigma 3 to isolate for removal and replacement of the cell fill lines of the Brent Bravo and Delta platforms based on the isolation methodology submitted.
An Experienced North Sea Partner
STATS had gained significant experience of working in the Brent Field based on our long involvement with providing isolation and testing services and addressing integrity issues including the cell fill lines and the import / export system of Bravo and Delta.
The scope was operated under the Shell Upgrade Project by a dedicated team known as the IMPACT Project. During its execution, it was the single largest project being undertaken by Shell in the North Sea. The original scope of work was to undertake the removal and replacement of all thirty two 10” NB cell fill lines situated within the utility shafts of the platforms, sixteen lines per platform.
The original plan was to isolate all sixteen lines at once but this strategy was reviewed and revised. Based on the overall risk, a single line at a time strategy was adopted.
Exacting and Challenging Scope
The cell fill lines connect the import / export manifolds to the individual storage cells of the gravity base structure. The only isolation device present for each line was a butterfly valve where the cell fill line was connected to the manifold. These valves were original items in place from the time the platform was commissioned and their sealing performance could not be guaranteed. The average cell fill line was approximately 30 metres long and each storage cell contains 10,000m3 of fluids, consisting of produced water, crude oil and a small volume of gas, at the time of project execution. In total across both platforms, an estimated 1,000 metres of piping was initially scheduled for removal and replacement.
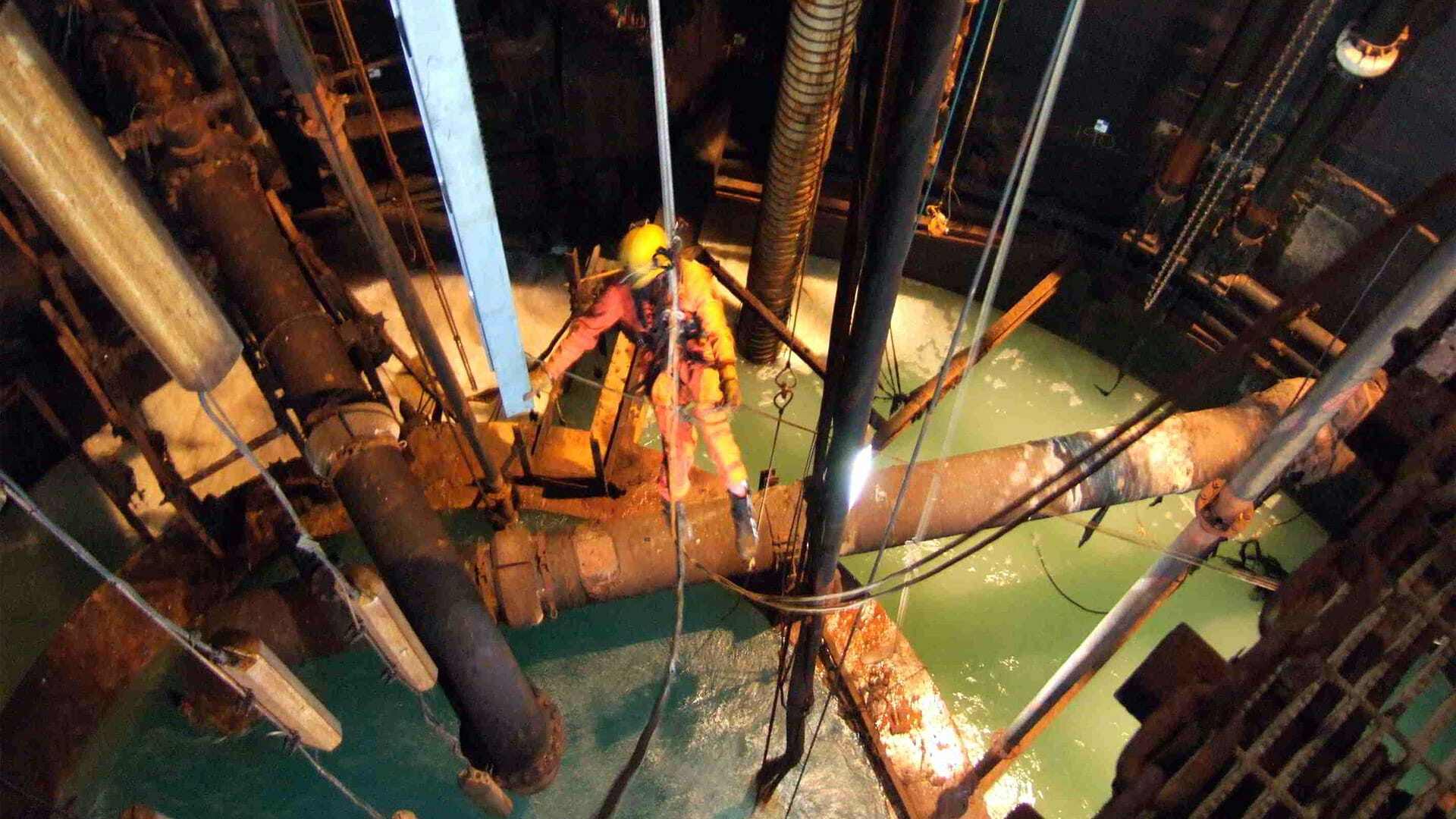
Fully trained rope access technicians perform operations on line-fed breathing apparatus
Unlike a typical isolation plug project whereby the plug is generally deployed via an existing plug launcher / receiver, or a temporary launcher mounted to a suitable valve within the system, the cell fill lines had no means of access into the lines. This scope required an entry into each line to be created first.
Considering existing hot tap technology, particularly line stopping methods, as a method of creating an access point and isolation, it was deemed that the robustness of the line stopping equipment was not acceptable to the project. This decision was based on the fact that line stopping utilises a single passive seal over which the operator has little or no control of the sealing performance.
A Powerful Combination of Innovation and Tenacity
STATS chose to implement their isolation philosophy of dual active seals with an annulus that could be used for test or bleed purposes, in essence a Double Block and Bleed (DBB) system.
This led to the development of the BISEP, the first stage of the isolation process, providing a barrier against the associated storage cell. However, this was an interim isolation to allow the formation of a full bore valved access point above the initial hot tap.
In reviewing the operation, it was considered that due to the condition of the manifold valves there was the clear potential that when venting and draining the line contents above the BISEP, the remaining fifteen cells could cross communicate the manifolds and continue to feed and pressurise above the BISEP.
An additional means of isolating the cell fill manifolds was required to ensure that the group of four cell fill lines were protected from the other cell fill groups. This led to the development of a floating polymeric grout material that would fill the manifold from the top down displacing inventory through the butterfly valves towards the cells. The polymeric grout was formulated to float in seawater. To try to formulate the grout to float in crude oil would have compromised the structural properties of the material. To ensure the manifolds were oil free, the cell group and manifold were exported to water prior to grout injection.
Filling from the bottom up had the potential to pressurise the manifold itself, which could only be managed by venting any pressure increase to production with an associated risk of affecting the fill profile in the manifold. Filling from the top down meant that during the grout injection process, no pressure increase could occur as the displaced fluids would be managed by the storage water make up system.
With the grout compound engineered, a means of actually deploying the material into the manifold was required. STATS extensive experience of pumping grout into repair clamps was reviewed and led to the detail engineering of the injection process to ensure the 1,500 litres per manifold was injected effectively. The manifold end flanges were hot tapped to provide injection and tell tale ports and a multi-pump arrangement was utilised injecting from both ends of the manifold. The injection process was both temperature and time constrained with a “point of no return” once the process was underway, careful planning and close liaison with platform operations throughout ensured the success of these scopes.
The cell fill manifolds were injected in pairs leaving two manifolds and associated cells available for ongoing production and export while the new piping system was connected to a reduced capacity new manifold system sited above the old import / export system in the utility shaft.
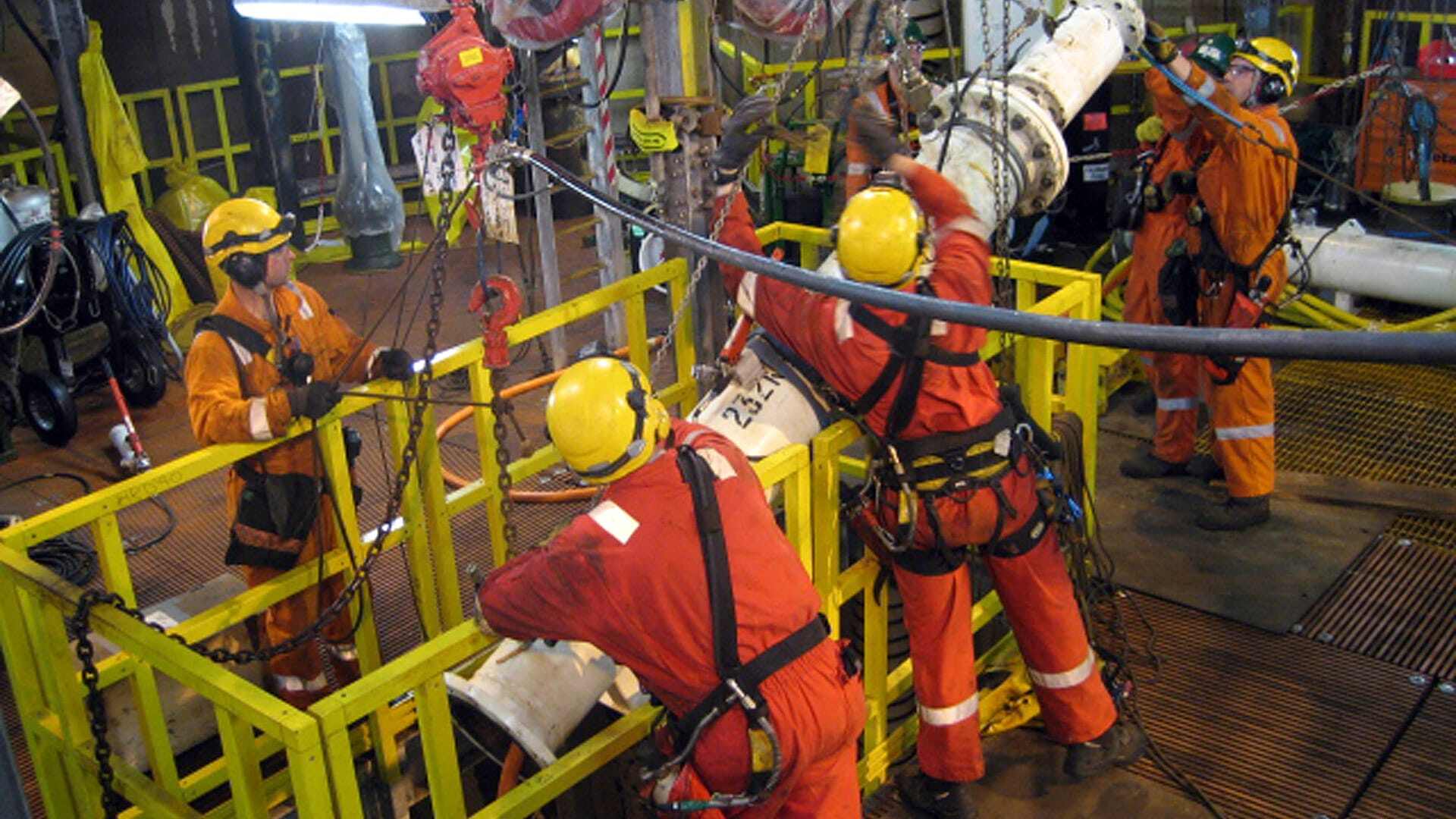
Second Phase Isolation Demands Further Innovation
The second phase isolation was engineered as a tethered isolation plug, a Tecno Plug, with the hydraulics and test functions operated through a five core umbilical. These Tecno Plugs were multi-module articulated items designed specifically for the operation using STATS isolation plug technology. The set location for the Tecno Plugs was the utility shaft penetration, a short section of piping cast into the concrete structure of the platform. A plug set at this location allowed all of the inboard piping to be removed.
Again, the Brents’ project posed unusual problems. To reach this set location the Tecno Plug had to be pigged through the cell fill lines which included negotiating bends. Isolation plugs are typically designed for pipeline service where the usual minimum bend radius is 3D. For the cell fill lines, where the piping was designed to ASME B31.3, the elbows were all long radius (1.5D) with Brent Delta having double elbows configured back to back and sometimes offset at 90°. Brent Bravo utilised single 1.5D elbows but had the added complexity of a spectacle blind (confirmed as reduced bore by camera inspection and UT measurement) directly between the utility shaft penetration and the elbow.
Meticulous consideration of every difference in detail
These slight, but critical differences in the platform piping required two distinctly different pigging disc and centraliser arrays to be developed for the Tecno Plugs, the devil was in the detail.
In addition to the differences of the lower piping arrangements for each platform, the utility shaft penetrations differed between platforms also. Brent Bravo had a reduced bore, coupled with a reduced length set area; the target for pigging to location was +/-100mm. Furthermore, should the set zone be overshot during pigging, the piping bore changed again, this time increasing as the pipework weaved its way across the cell roof structure. Brent Delta has a continuous bore with a much longer potential set location.
As a further restriction to the operation, a pigging pressure limit was imposed to prevent any damage being caused to the lines or any of the existing repairs, significant onshore trialling allowed the pigging disc arrays to be fine tuned to minimise the pigging pressure requirement and also verified the reliability of the system.
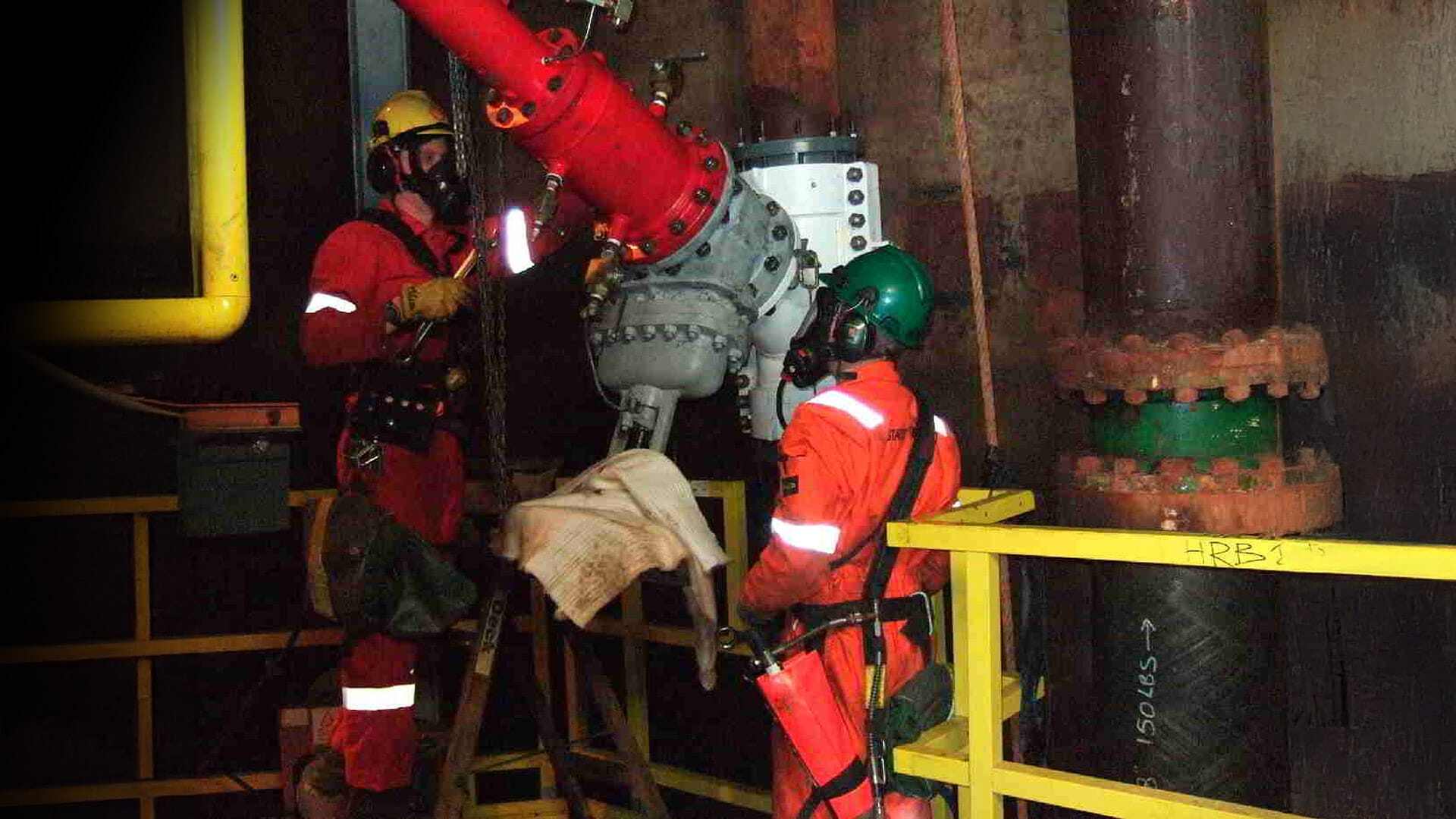
Engineers draining splitting machine on BA after cutting coupon
An additional service that was utilised was an inspection camera to confirm the bore condition of the penetration. As these lines were Brownfield, and had been out of service for some time and had been hot tapped, it was felt that some visual survey data would be beneficial prior to the deployment of a Tecno Plug. Preliminary camera inspection runs highlighted the presence of swarf and scale debris within the penetrations. This would have likely proved to be detrimental to the sealing performance of the Tecno Plugs. To address this by conditioning the line, gel pigs and a debris suspension gel system was deployed to remove the contaminants and flush them into the cell. After the gel pig run had been completed, the camera was redeployed to confirm the penetration was clear of any debris.
As the piping was Brownfield, the possibility of not being able to achieve a leak tight seal was considered. Although all of the onshore trialling and verification had been performed in test fixtures constructed using sections of old piping removed from Brent Charlie with excellent performance, the real deployments may not have been so effective. To ensure project progression, an isolation bypass acceptance criteria was developed. This criteria was supported by analysis software that could assess, quantify and verify the isolation performance ensuring that the isolation was safe and within project acceptance criteria prior to any breaking of containment.
The whole scope was performed with both platforms in full production including individual cells isolated with destructed pipework while export was ongoing.
Extensive, Realistic Training for Safety at Every Level
The early development and testing of the isolation tooling had necessitated the fabrication of various test fixtures. However, as the enormity of the task ahead became increasingly apparent and the need to implement the scope with a multi-disciplined offshore team, personnel safety was always considered paramount.
The scope was to be executed in a confined space environment (the utility shaft) some 70 metres below sea level. To this end, a large scale test fixture was developed and fabricated to provide representative piping and conditions of both Brent Bravo and Brent Delta. This test fixture allowed the offshore teams to perform full scale operations in realistic conditions, i.e. on ropes, wearing Breathing Apparatus and using radio communications, the training highlighted the physical demands of the operation and the need for a high level of fitness for all personnel involved. In fact just getting to and from the worksite involved negotiating approximately five hundred stairs. The in-depth onshore training programme was developed to cover every aspect of the offshore scope, including third party specialist instruction for the onsite machining equipment.
In total, approximately 80 people (both shifts from both platforms) completed the onshore training programme (the full offshore team from technicians to construction superintendents). In addition to the core operation, specialist onsite machining was involved and the Rope Access technicians also attended OEM training.
The main training programmes were also witnessed by OIM’s, Offshore Supervisors, Project Team Leaders, Technical Authorities and the Project Engineering Team. Attendance and completion of the onshore training was deemed a pre-requisite for being included in the offshore team.
Adapting to a revised reinstatement strategy
As the project progressed offshore, the platforms were nearing their End of Field Life, with Brent Delta proposed as the first platform targeted for Cessation of Production.
The original strategy of replacing all of the lines was reviewed. Considering the reduced production profile of both platforms the reinstatement strategy was revised. This new strategy meant that only four cell fill lines were to be replaced which was considered sufficient for platform production purposes. The redundant cell fill lines would be isolated and disconnected from the redundant manifold system leaving each individual line with a full bore valved entry point for any subsequent access requirements as required by the Decommissioning Project for any cell sampling or remediation works. The manifolds were fully capped using STATS weldless mechanical connectors.
On completion, the project end state left all of the original manifolds and pipework completely isolated from the final hydrocarbon production system of the platform. The new cell fill lines and manifold system are the only piping carrying hydrocarbons in the shaft.
For the duration of the project, the STATS team had no Lost Time Incidents (LTI’s), a commendable achievement and a reflection of the professionalism of the whole team and their attitude towards delivering a quality project in a safe and effective manner.
More hot tapping has been used on this project than in the whole of Shell’s previous history and the pioneering plugging technology has been pivotal. Above all the project’s six month safety and competency training programme is second to none.

Shell
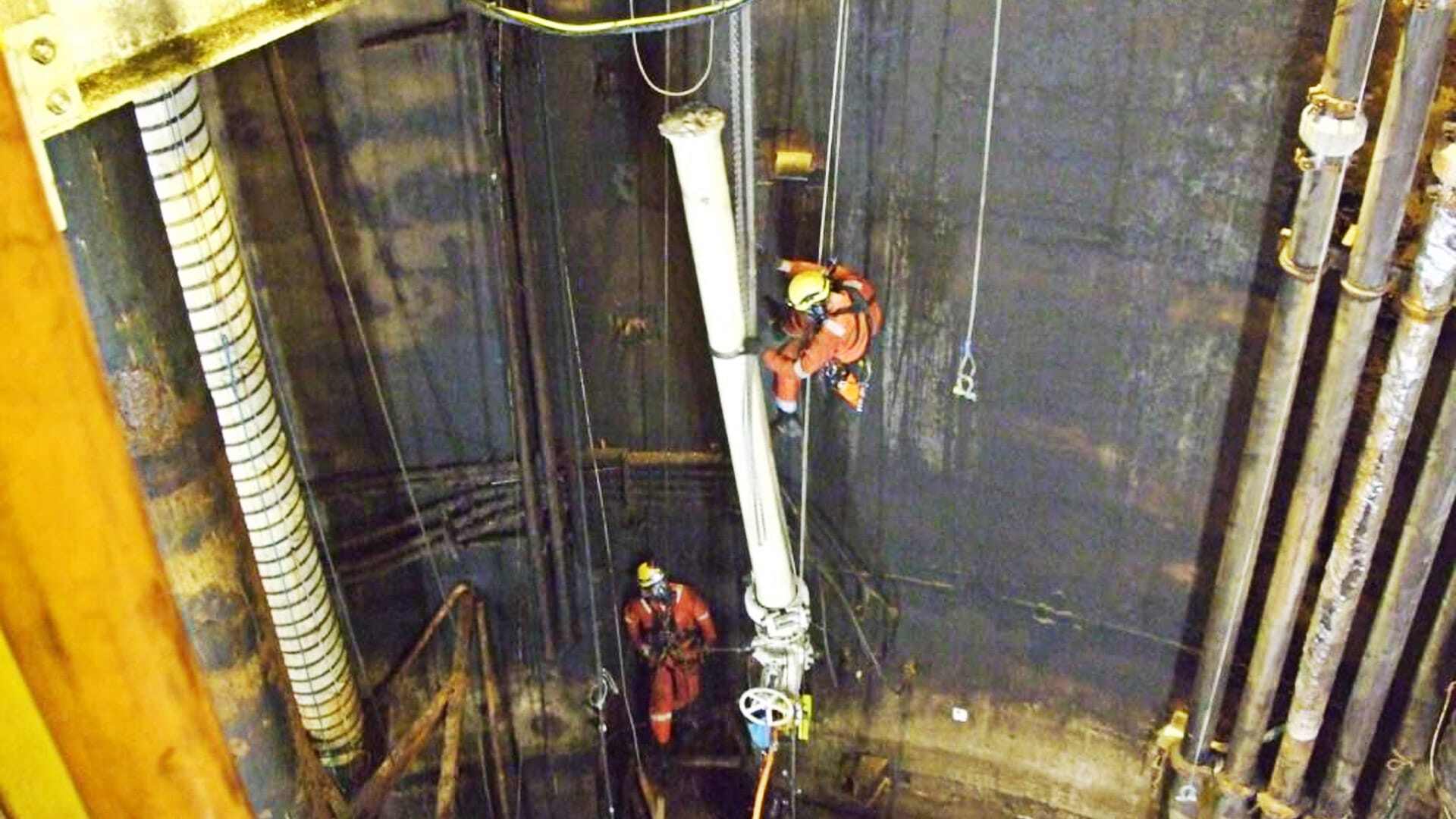