Case Study
14” 2500# Subsea Mechanical Connector, North Sea, UKCS
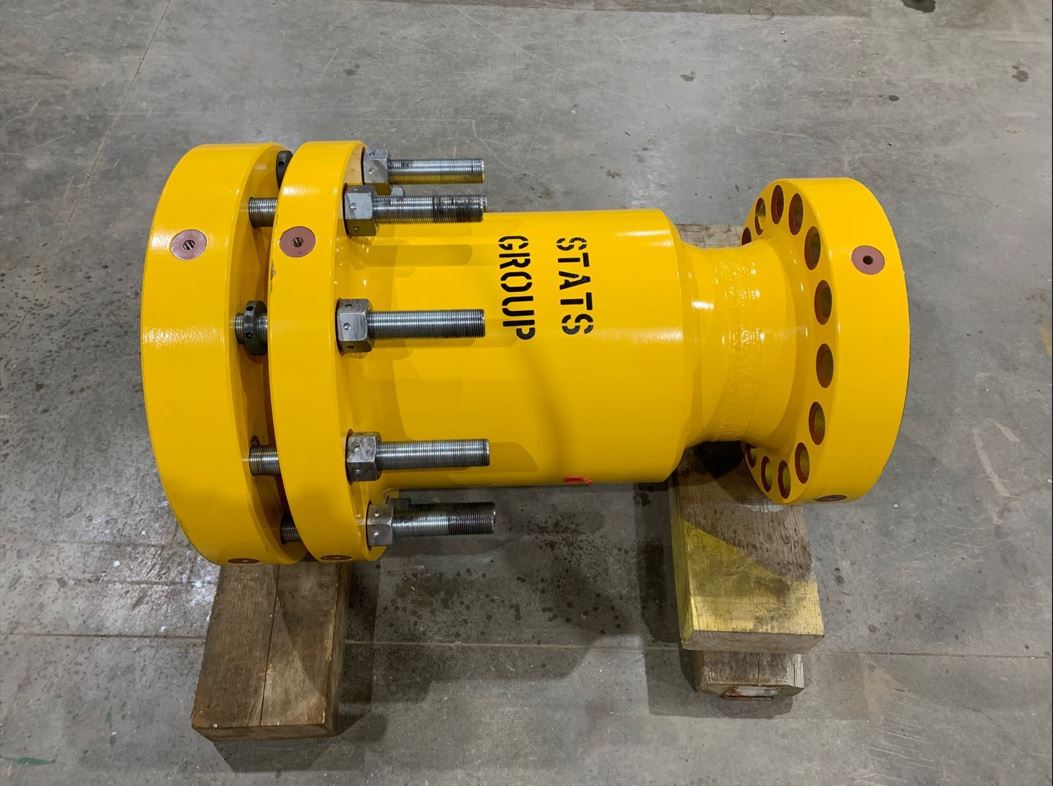
STATS Group provided two class 2500 subsea mechanical connectors as part of a subsea flange repair project in the North Sea, UKCS.
STATS Group were contracted by an oil and gas operator to provide two class 2500 subsea mechanical connectors as part of a subsea flange repair project in the North Sea, UKCS.
While conducting the offshore installation phase of a new field development, spool pieces were installed and the piping infrastructure was leak-tested, at this stage an integrity issue was identified. During leak-testing damage was discovered on the sealing face of the platform riser base flange, allocated for the tie-in of the pipeline. At this stage the operator put plans in place to carry out an in-situ repair of the damaged flange. However, in case the repair was unsuccessful a contingency solution was developed. This solution would allow the damaged flange to be cut and removed and replaced with a 14” class 2500 mechanical connector, installed directly onto the bare pipe end. This would ensure the schedule for commissioning the new pipeline would not be jeopardised if the subsea flange repair failed.
The project required two mechanical connectors to be provided, as for technical assurance, one of the connectors was subject to bend fatigue testing, and as the fatigue test was a test to destruction, the primary connector could not be used. A factory acceptance test was carried out on both connectors before they were shipped to a third party for the bend testing. All stages of the connector manufacture, assembly and testing was witnessed by an independent verification body and the client.
Following the successful repair of the platform riser base flange the connector was not required and installation was not needed. However, the connector is now stored for the client in a state of readiness for any future planned or emergency repair scenarios.
In operation the connector is offered onto the pipe end and a seal compression flange is actuated to set the seals. The seals are then pressure tested to prove the integrity of both seals, prior to setting the locks. Once the seals are verified, the lock bowl is actuated, by torquing a separate array of bolts to set the locks onto the pipe. Each lock segment is individually torqued to ensure even circumferential grip load around the host pipe and eliminating excessive stress and unacceptable strain of the pipeline. A final localised code-compliant strength test and seal leak test verifies that the connector is structurally secured to the pipeline and the seals are leak tight. An environmental seal is included in the compression flange to allow the lock cavity to be flushed with an inert fluid.
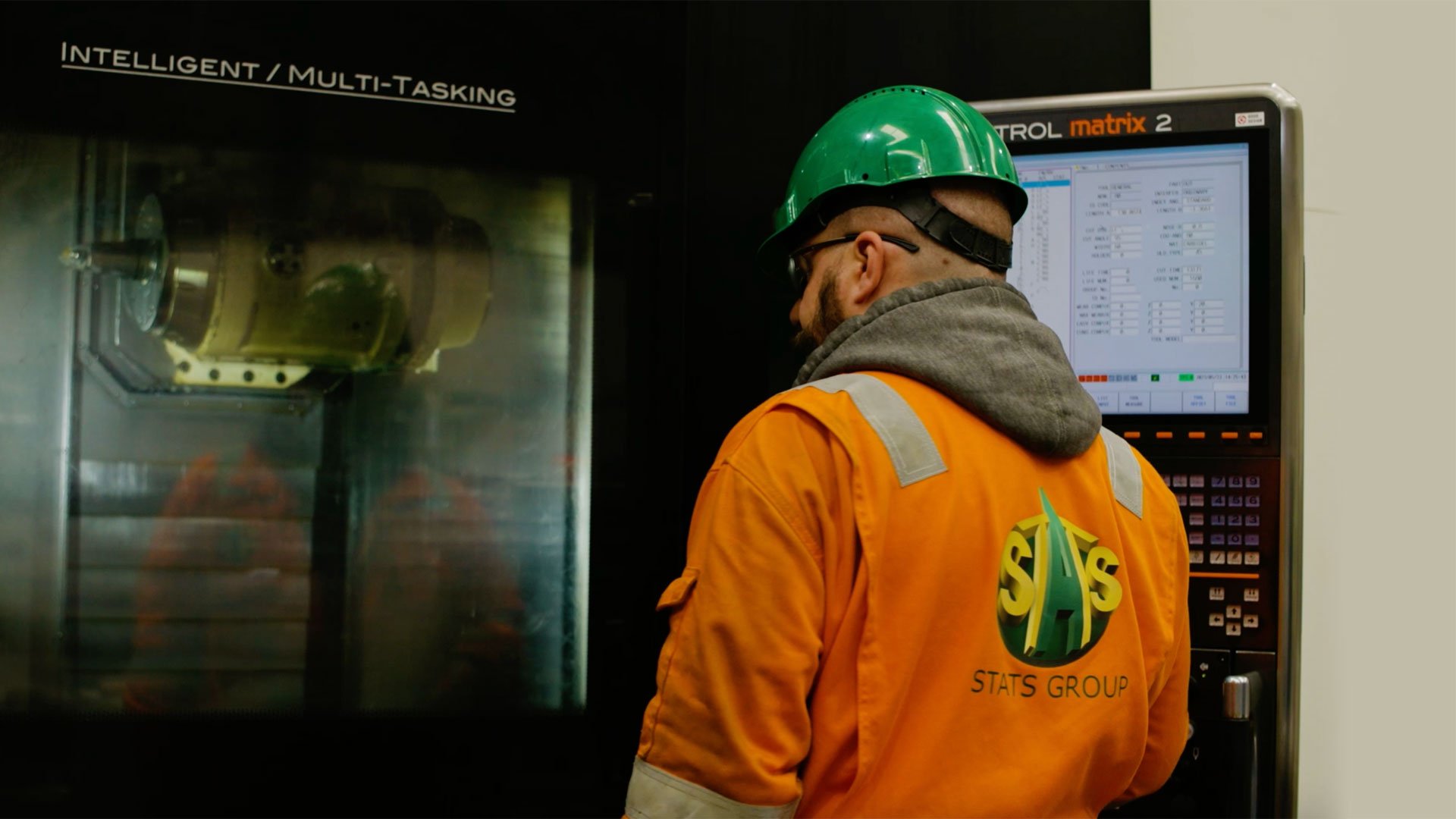