Case Study
24” Caisson Liner 95m Long | Piper Bravo, North Sea, UK
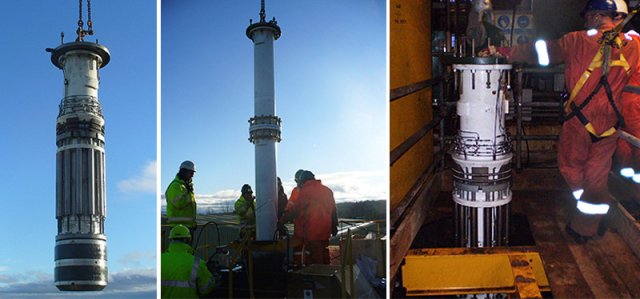
Caisson Liner during factory acceptance testing and offshore installation
Background / Challenge
- Requirement to install a liner into an existing 98m long 24” OD caisson, to accommodate water discharge
- Requirement to seal caisson / liner annulus space
- The caisson could not be replaced due to worksite height and deck level restrictions
- Caisson Liner required internal corrosion resistance
- Caisson Liner must pass caisson bore restriction at waterline
- Caisson Liner had to accommodate thermal expansion
Solution
- Carbon Steel spools manufactured in suitable lengths to allow for space restrictions on installation deck
- Overall finished length of liner 95 metres
- Spools internally clad with Inconel 625 to address internal corrosion issues
- Hydraulically operated dual seal and lock arrangement on base section of liner
- Lower liner spools with reduced 14” OD slip-on flanges in order for spools to pass the bore restriction
- Liner upper section allowed for thermal movement with a sliding sleeve arrangement
- 8 off Inconel control, actuation and injection lines incorporated
- In-house assembly of the whole liner to check for straightness and flexibility
- Successful completion of the job safely and ahead of schedule
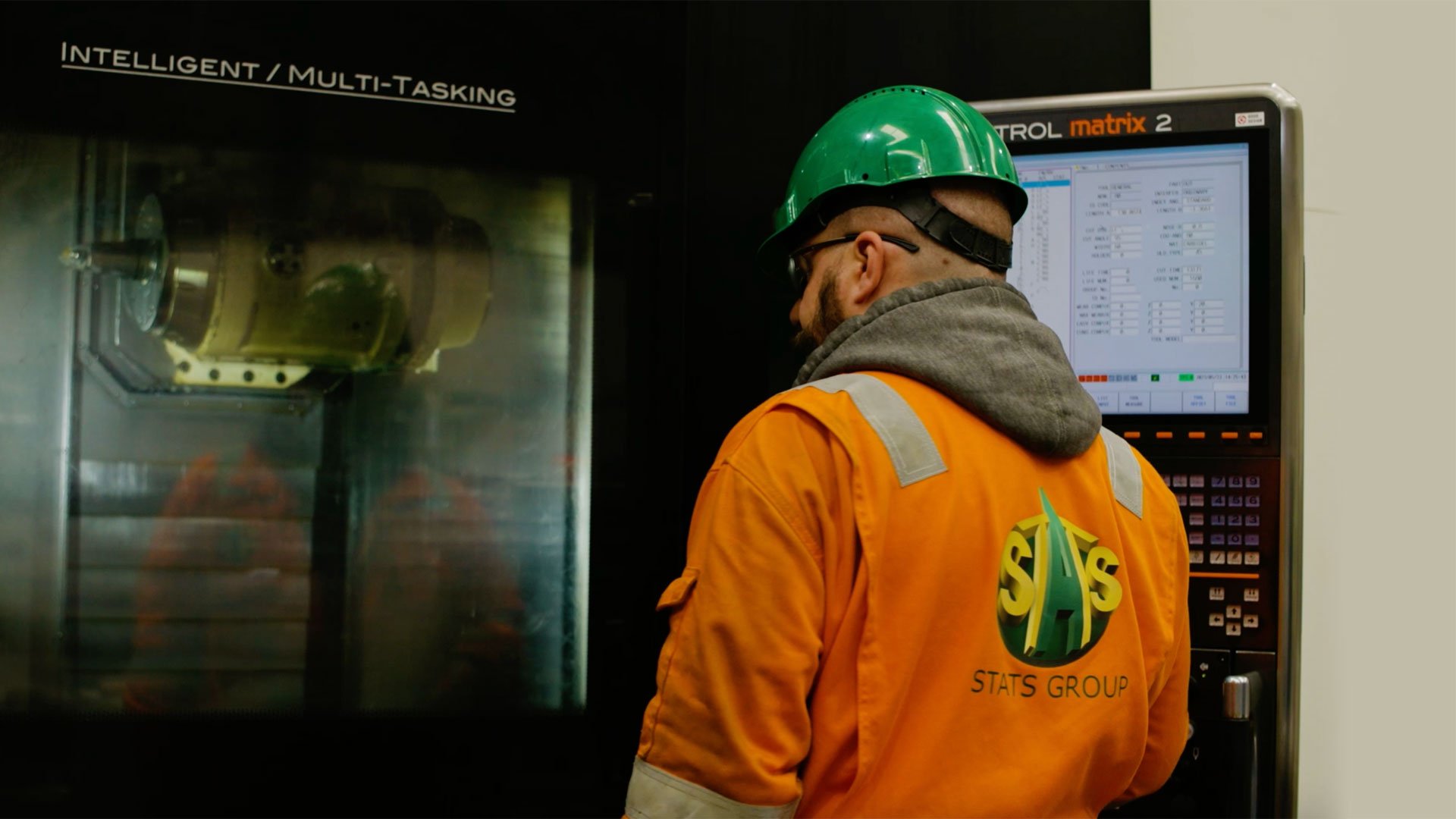