Case Study
3” BISEP™ & Tecno Plug™ | Tern Alpha Platform, North Sea, UK
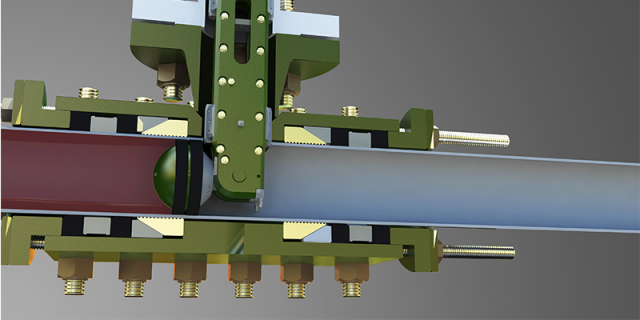
TAQA Bratani Ltd required an isolation solution to facilitate pipework replacement of a 3” instrument air line on board the Tern Alpha Platform without the necessity for a platform shutdown. STATS Group proposed the use of a 3” BISEP™ and 3” Tecno Plug™ to provide a double block and bleed (DBB) isolation. To allow deployment of the BISEP™, full bore access was obtained by hot tapping into the live line by using a STATS supplied mechanical tie-in clamp and ball valve.
Once hot tapping operations were complete and the pipe coupon was recovered into the hot tap machine, the ball valve was closed allowing the hot tap machine to be removed. The BISEP™ was then fitted to the ball valve, housed in a pressure competent launcher. Leak testing of the launcher confirmed pressure integrity allowing the ball valve to be opened and the BISEP™ deployed into the pipework towards the flow to be isolated.
Hydraulically setting the BISEP™ compresses the spherical head and the resultant radial expansion pushes the seals out against the pipe bore. The twin compression seals provide a facility to bleed and monitor the intermediate annulus. The seal annulus port proves and monitors the seal integrity before and during intervention work.
After performing validation tests on the BISEP™, STATS confirmed successful double block and bleed isolation and an isolation certificate was issued to the client. The pipework was then cut and removed from behind the BISEP™ with a clamshell cutter. In order to allow removal of the clamp and hot tap penetration from the system, STATS then installed a temporary launcher with a pre-installed 3” Tecno Plug™. This allowed the BISEP™ to be retracted and the Tecno Plug™ to be deployed and set beyond the hot tap penetration to provide a new double block and bleed isolation barrier.
On verification of the Tecno Plug™ isolation, the tie-in clamp, ball valve and BISEP™ assembly was removed from the air line, the pipework was then cut to remove the hot tap penetration while the Tecno Plug™ provided isolation.
To allow a tie-in point for the new valve and pipework, a mechanical flange was fitted to the cut pipework behind the Tecno Plug™. A valve and temporary launcher were then attached and strength pressure-tested against the back of the Tecno Plug™ to confirm integrity of the new flange joints and mechanical flange.
The Tecno Plug™ could then be unset and retracted into the temporary launcher and removed with the new valve providing isolation and allowing replacement pipework to be connected, completing the operation. Two STATS technicians carried out the entire workscope within five days, including the cold cutting and hot tapping activities while the system remained fully operational. STATS multi-disciplined technicians routinely perform complete workscopes including additional onsite machining services such as hot tapping, cold cutting or flange facing services, resulting in reduced costs and accommodation requirements for the operator.
Paul Davies, Project Manager at STATS Group, said: “The BISEP™ dramatically increases safety over traditional line stop methods, while the dual compression seals are more compliant than traditional cup seals, particularly in mature pipework that may suffer from pitting or corrosion.
“Operators can make significant savings by performing maintenance or repair work without the need for a shutdown. The single entry point of the BISEP™ reduces costs and operational timescales by providing a verified double block and bleed isolation through a single intervention point, without the need for additional bleed ports.”
Download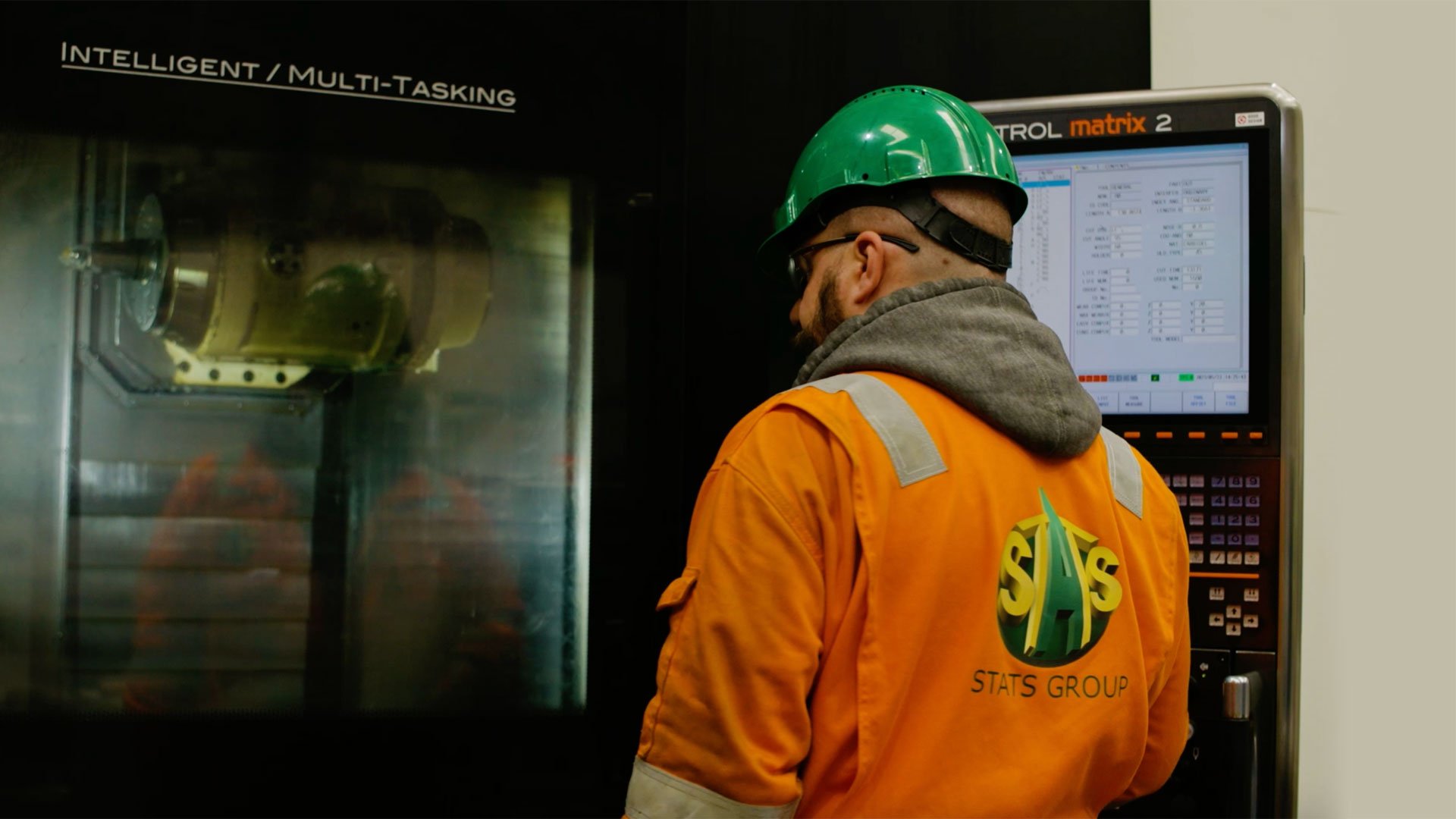