Case Study
4" Hot Tap and Line Stop (BISEP®) For Oil Flowline Recommissioning
Tool - BISEP Plugging Tool, Fittings
Location - Papua New Guinea
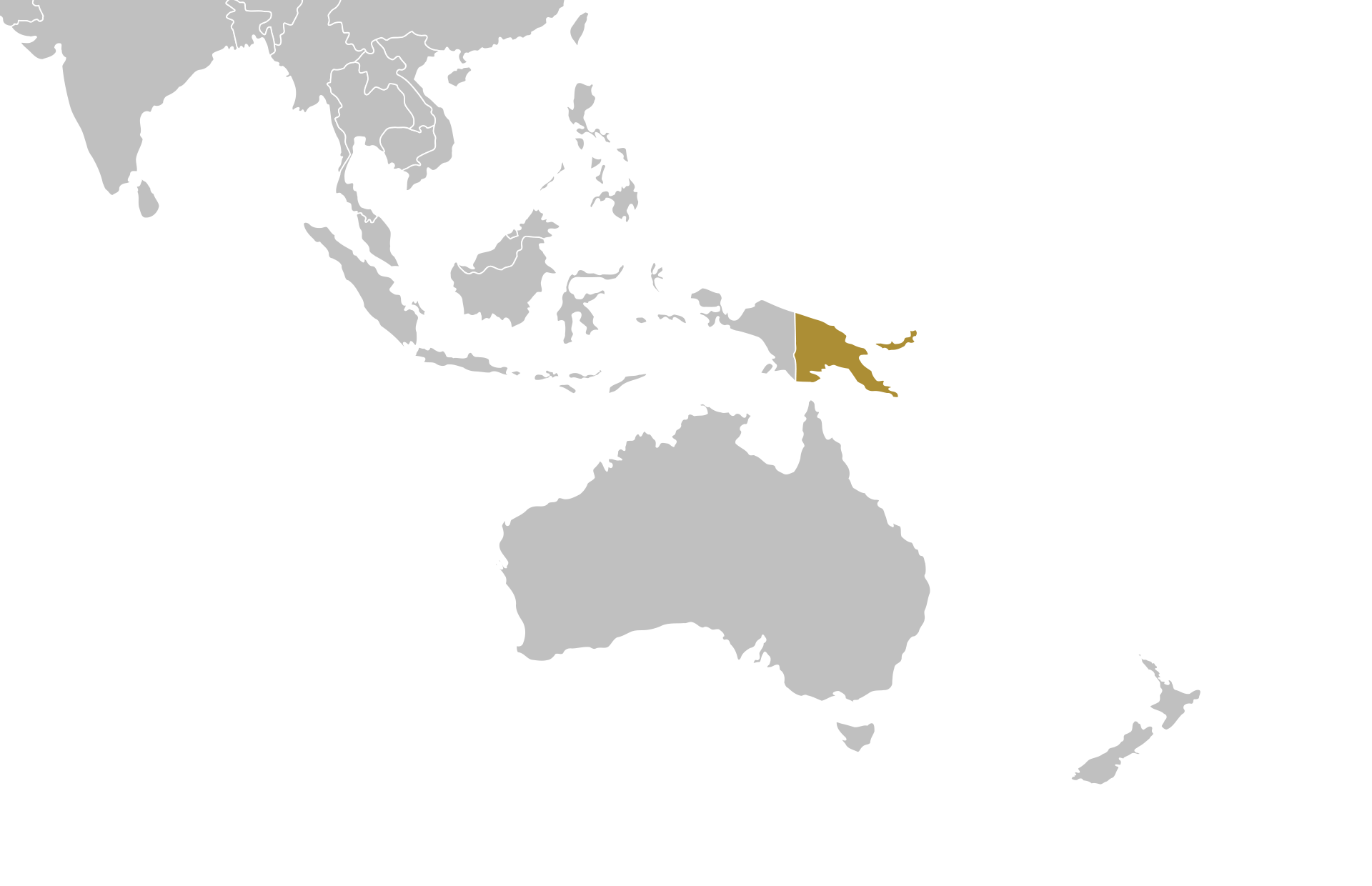
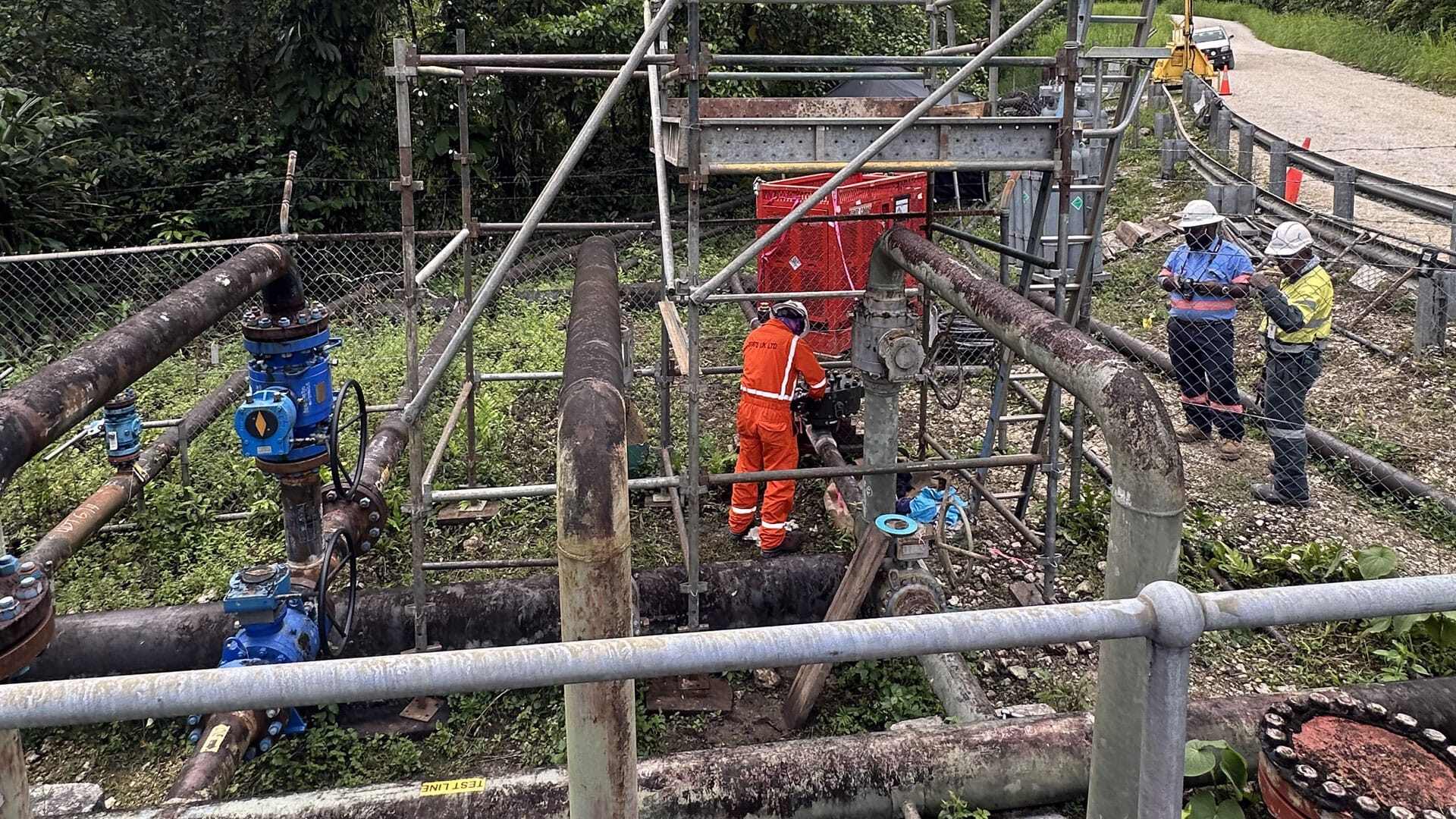
A challenging remote location at high altitude in the southern highland mountains of Papua New Guinea was the destination for STATS Group’s 4” Hot Tap and Line Stop (BISEP®) project.
Line Stop and Hot Tap Expertise for Complex Oil Flowline Recommissioning
STATS were contracted to provide fitting supply, hot tapping and line stopping services on a redundant 4” oil flowline that required recommissioning in order to be reinstated back into service.
STATS BISEP® line stopping tool was utilised to provide safe worksite conditions and avoid any discharge and pressure release to the environment and personnel during the break of containment activities. The leak-tight isolation allowed the pipe to be cut, then two flanges welded onto the pipeline where a valve manifold was positioned between the two flanges into the pressurised flowline permitting a 128 bar hydrotest to be conducted prior to reinstatement, to confirm the line could operate safely at its maximum allowable operating pressure.
In addition to the provision of the BISEP line stop tool, slab valve and hot tap machine, STATS manufactured and supplied the fitting and completion plug, along with providing STATS trained and competent field technicians. All STATS’ supplied equipment was tested and certified prior to mobilisation to site and in line with the project parameters to confirm full functionality.
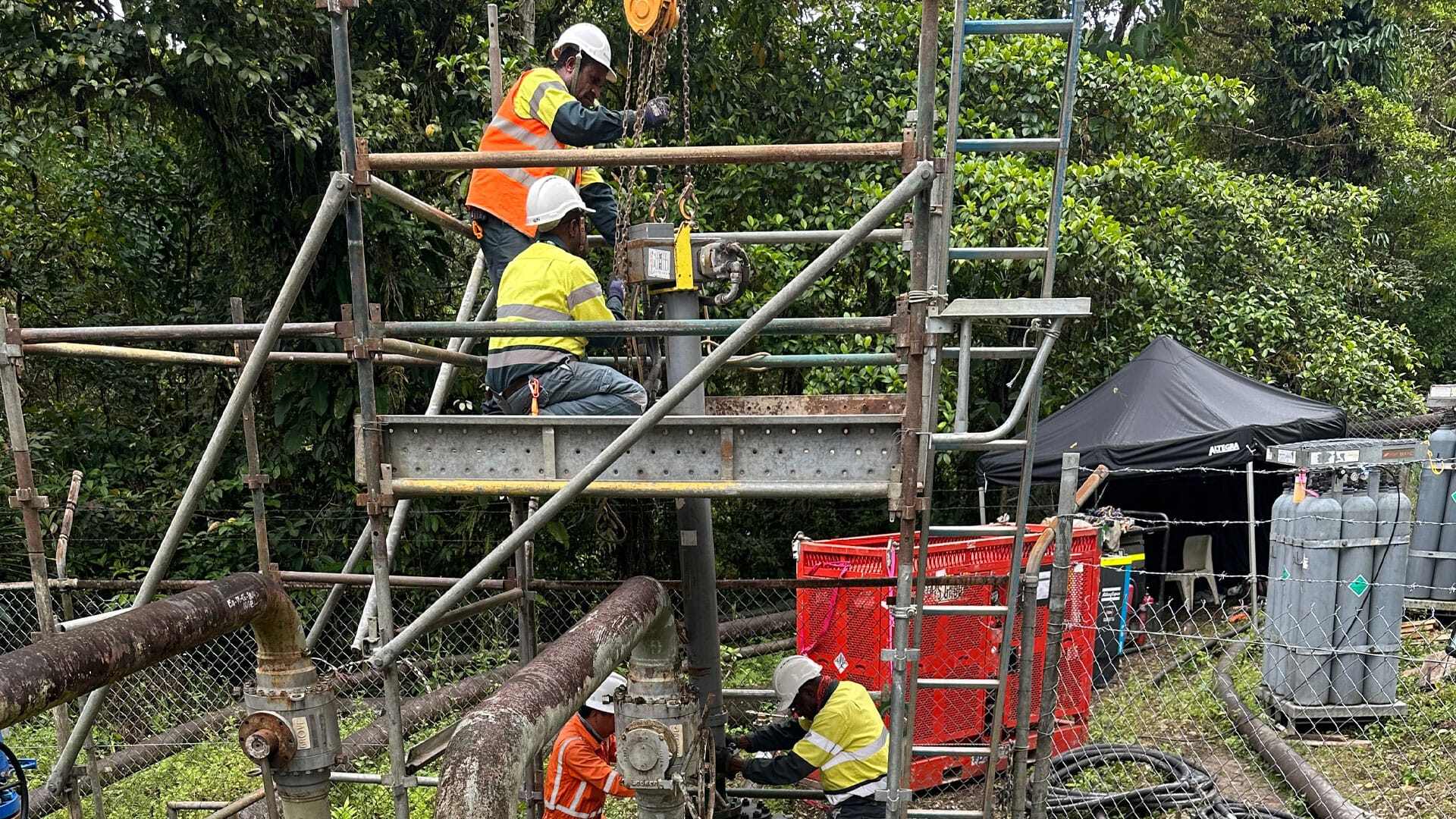
A Remote Location Surrounded By Vital Community Infrastructure
The worksite was situated next to a busy road which provided access for the crane to deliver the equipment to the site location which proved a challenge due to operational and local traffic in the vicinity with both the client and STATS managing traffic when lifting operations were being carried out. This was completed safely with no interruption to traffic or risk to the local community.
Once at the worksite the fitting was welded onto the pipeline and tested. STATS conducted the hot tapping, recovering the coupon and installing the BISEP ready for deployment. In order to move the metal cuttings (swarf) from the isolation section of pipe, the BISEP head was deployed into the line to sweep the line and displace the swarf prior to redeploying the BISEP and hydraulically setting the plugging head.
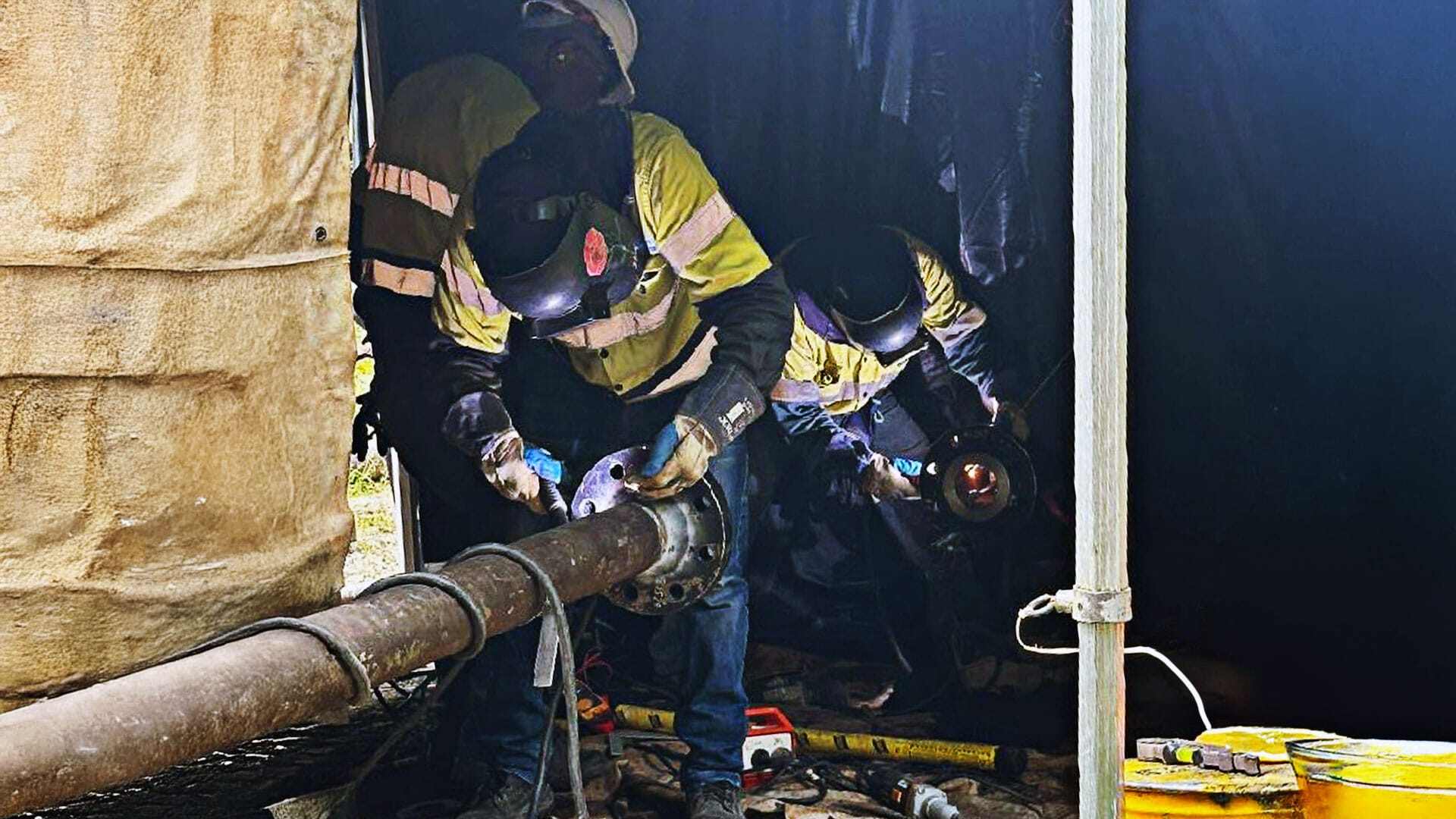
Fail-Safe Isolation Successfully Completed
When setting the BISEP, the plugging head expands the dual seals and causes them to radially expand and contact against the internal diameter of the pipe wall. Hydraulic activation allows for high integrity sealing and is beneficial in ageing pipelines where internal issues such as pitting or ovality may be present.
During the setting process, the pressure within the annulus (between the primary and secondary seals) rises as the annular space is compressed by the expanding seals. This pressure is monitored to prove no pressure loss and provide an initial indication that the seals are isolating, allowing the client to depressurise and drain the line. Once the line is depressurised the differential pressure across the BISEP plugging head maintains isolation independent of the hydraulic pressure, providing a fail-safe isolation.
“Another successful project completed in Papua New Guinea with the high altitude (4200 ft) conditions challenging at times, however the BISEP performed flawlessly. The project was completed safely and 5 days ahead of schedule which provided significant savings for the client”.

Rab Milligan
Testing and Certification
When the isolated section of line is drained the BISEP secondary seal is tested above the pipeline pressure to prove the integrity of the secondary seal. The seal annulus is then vented to a safe area and locked-in. This allows the primary seal to be tested and monitored for sealing performance. When the secondary and primary seal tests are complete, STATS issue an isolation certificate to confirm leak-tight double block and bleed isolation, allowing the break of containment activities to commence safely. The BISEP is the only hot tap installed isolation tool on the market that satisfies the design criteria for DNV Type Approval for Pipeline Isolation Plugs.
Upon completing the welding of the flanges NDT tests were conducted and when confirmed, the valve manifold was installed into the pipework.
- The BISEP is the only hot tap installed isolation tool on the market that satisfies the design criteria for DNV Type Approval for Pipeline Isolation Plugs.
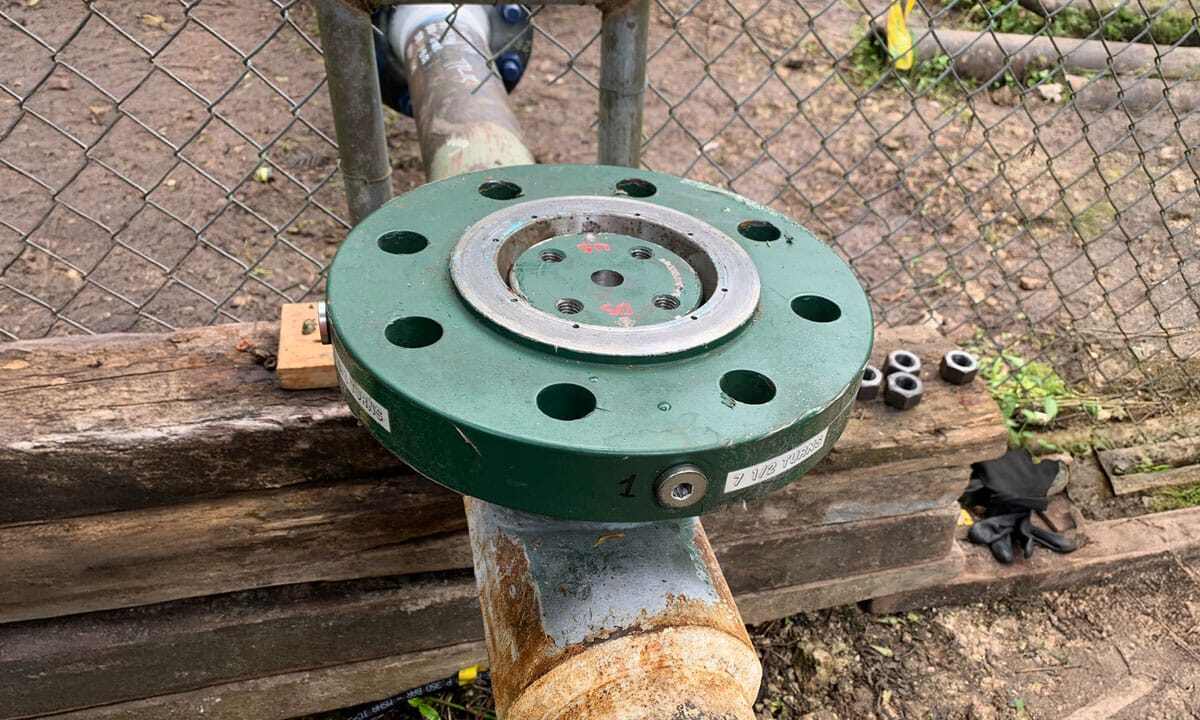
Workscope Completion - Five Days Ahead of Schedule
With the client workscope completed the line pressure was equalised and the BISEP was hydraulically unset and recovered from the line. A blind flange was then installed onto the slab valve to allow the client to conduct a pressure test of both ends of the pipework between the valve, which confirmed the valve was not passing before start up. STATS utilised the slab valve and their manifold configuration to assist the client with pressure testing the pipeline.The unique design of the STATS slab valve allows it to be used as a pressure retaining valve and as an operational device to help the client safely reroute pressure within the pipeline. STATS then redeployed the Hot Tap Machine to deploy and set the completion plug, marking the end of a successful project.
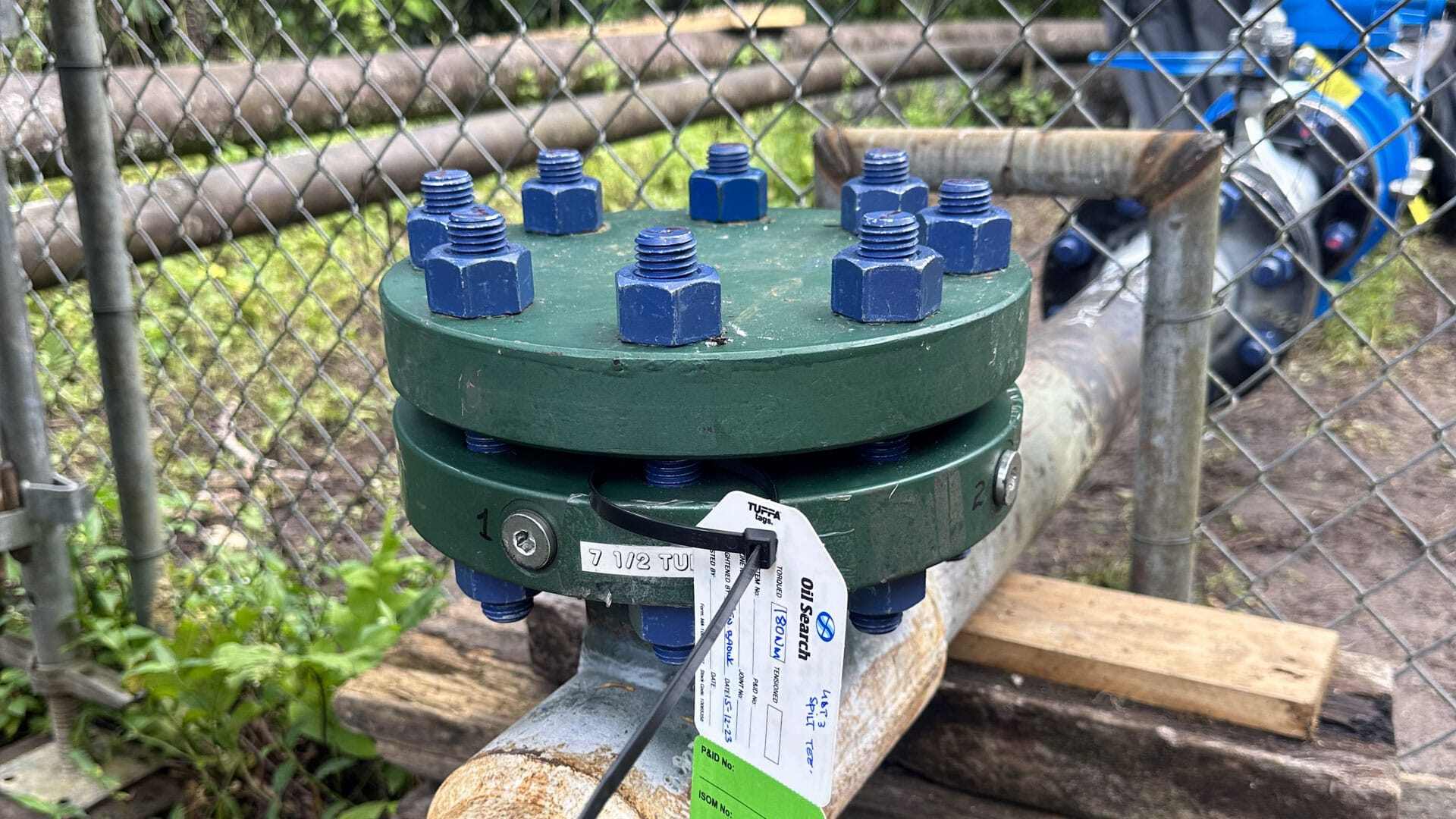
This project is another significant milestone for STATS as we expand our presence to support pipeline operators in Papua New Guinea and the wider Asia Pacific region. The BISEP provided fail-safe, double block and bleed isolation through a single hot tap penetration, increasing safety while also reducing the number of fittings and associated welding and hot tapping activities. We are delighted to demonstrate our market leading line stop technology in the PNG market and look forward to future projects with this valued client

Gareth Campbell
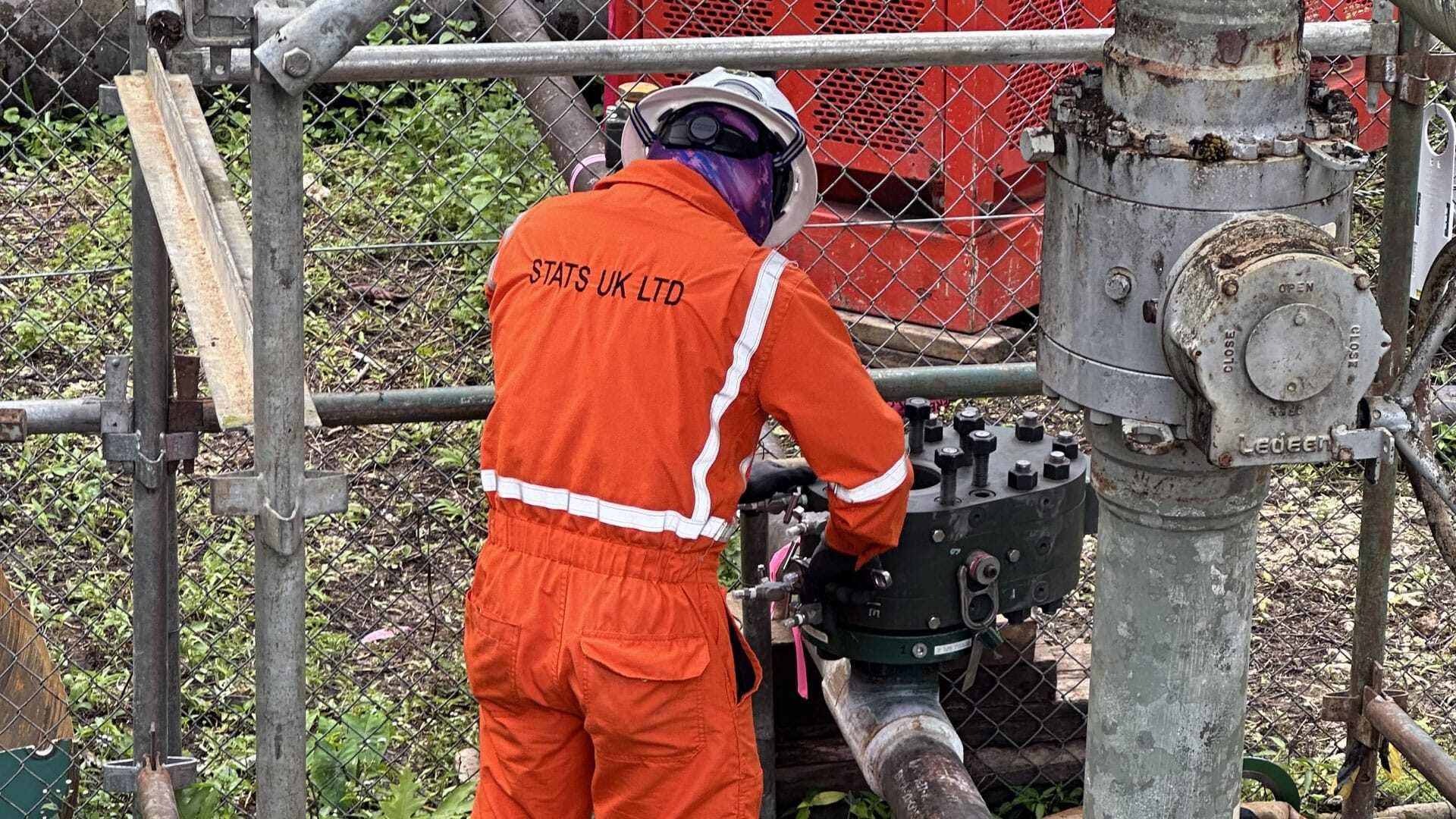