Case Study
8” Subsea Pipeline Isolation & Repair, Gulf of Thailand
Tool - Subsea BISEP Plugging Tool, Subsea Hot Tap Clamp, Subsea Mechanical Pipe Connector, Subsea Abandonment Plugs
Location - Gulf of Thailand
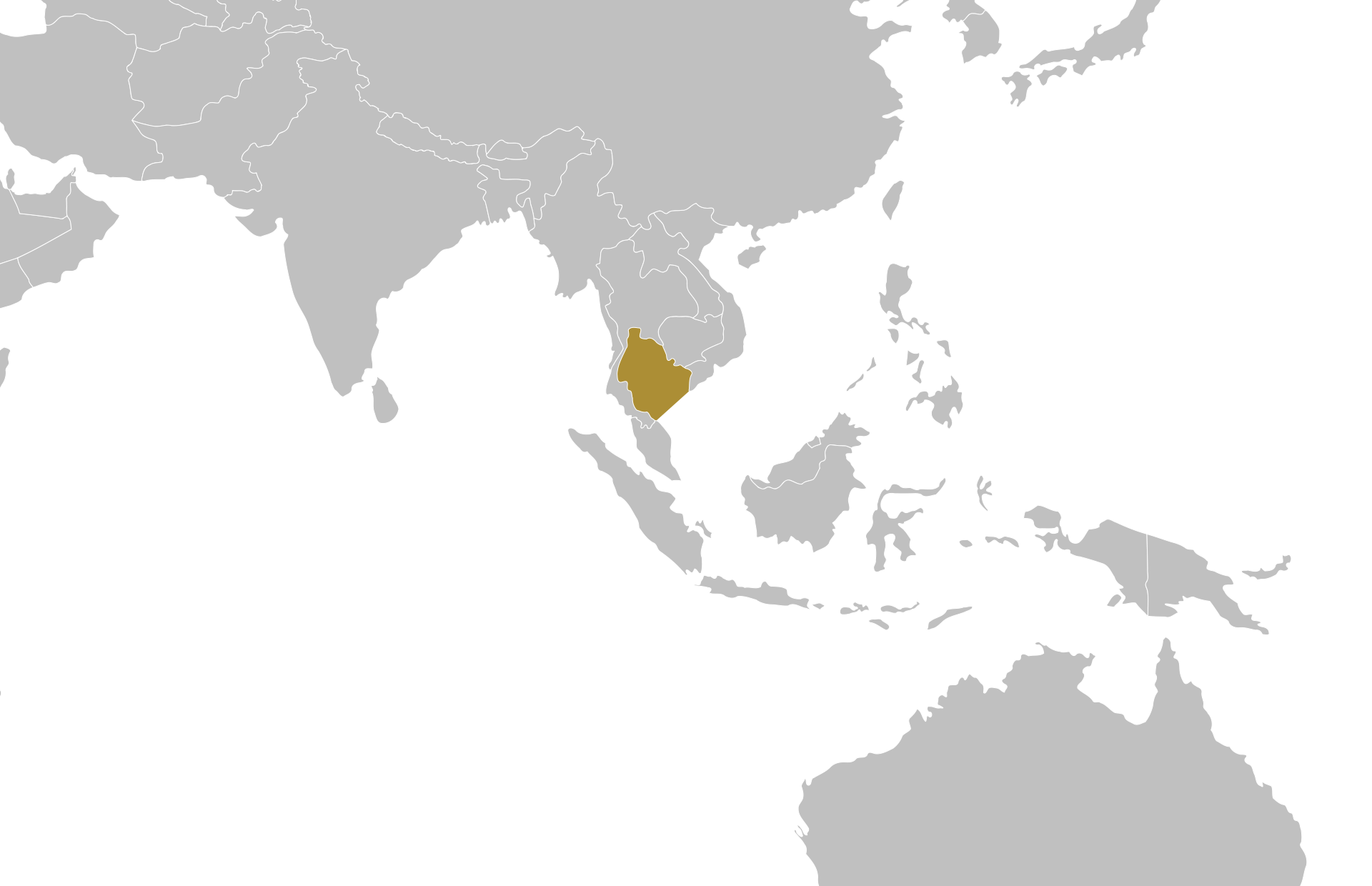
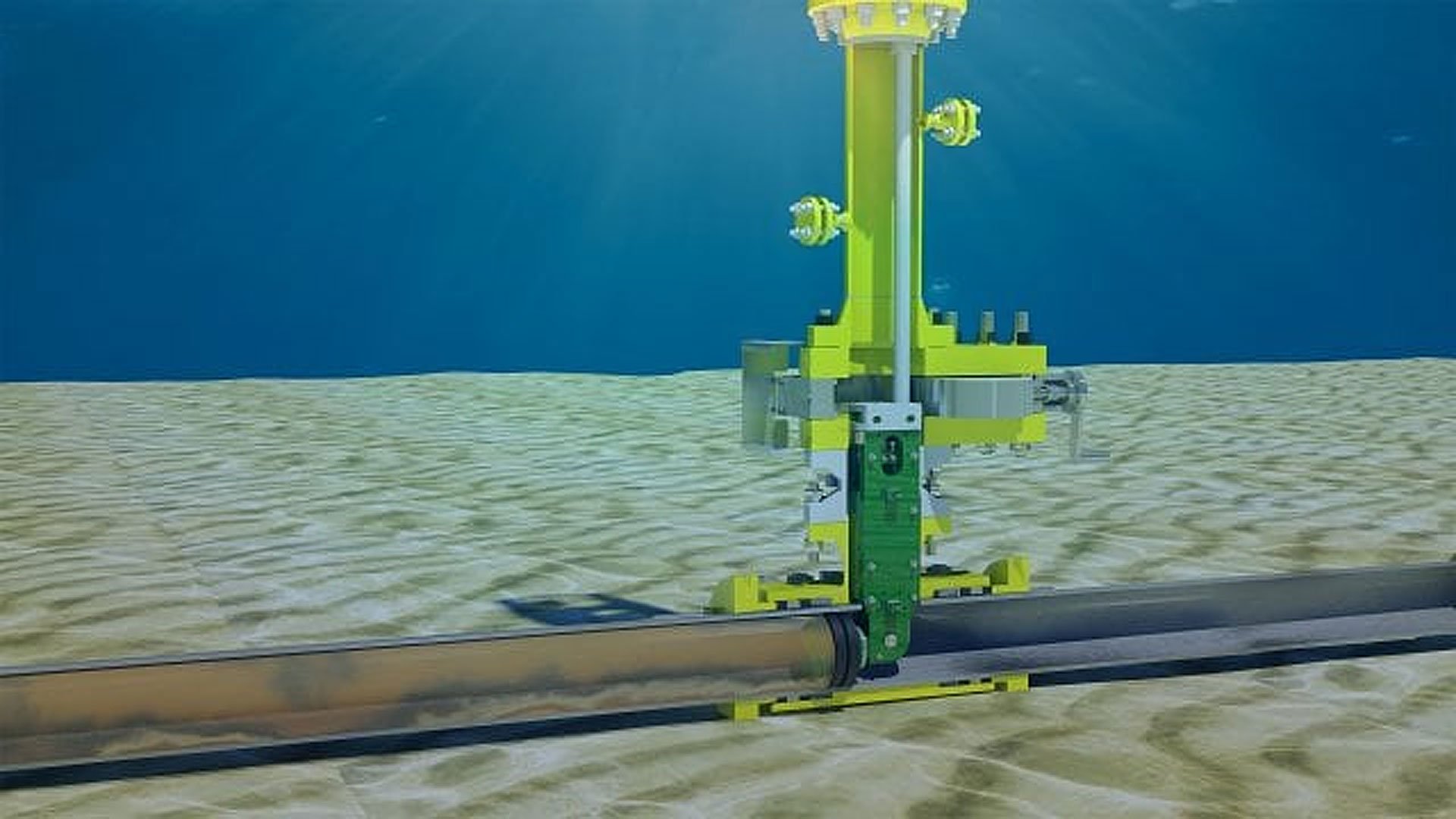
Subsea BISEP deployment
STATS Group was engaged by CUEL Ltd to address physical damage to a specific section of an 8” gas condensate export pipeline in the Gulf of Thailand. This damage was quite significant: the pipeline section had been dragged by a vessel anchor approximately 8 meters out of its original position and required a permanent repair.
The challenge was to execute this repair on a live, pressurised pipeline operating at 60m water depth and under pressures ranging from 7 to 21 bar.
Subsea Innovation: Bypass Repair Without Depressurisation
The key constraint was the requirement for the damaged section to be isolated and safely removed without impacting production or the environment, and crucially, without risk to diver safety. It was this specific context that required a complex intervention involving isolation tools and a bypass, rather than a simpler method that might involve depressurising the entire line.
STATS utilised its range of subsea products to facilitate the repair, which included BISEP’s, slab valves, hot tap fittings, completion plugs, end connectors and abandonment plugs. This comprehensive suite of tools was engineered, manufactured, tested by STATS, prior to deployment in-field, allowing the pipeline repair to be successfully completed in December 2016.
Following a detailed engineering and risk assessment by CUEL and the pipeline owner, a repair methodology and solution was developed, whereby an 8” bypass was installed on the seabed as a permanent repair to re-route the pipeline medium away from the damaged pipeline section.
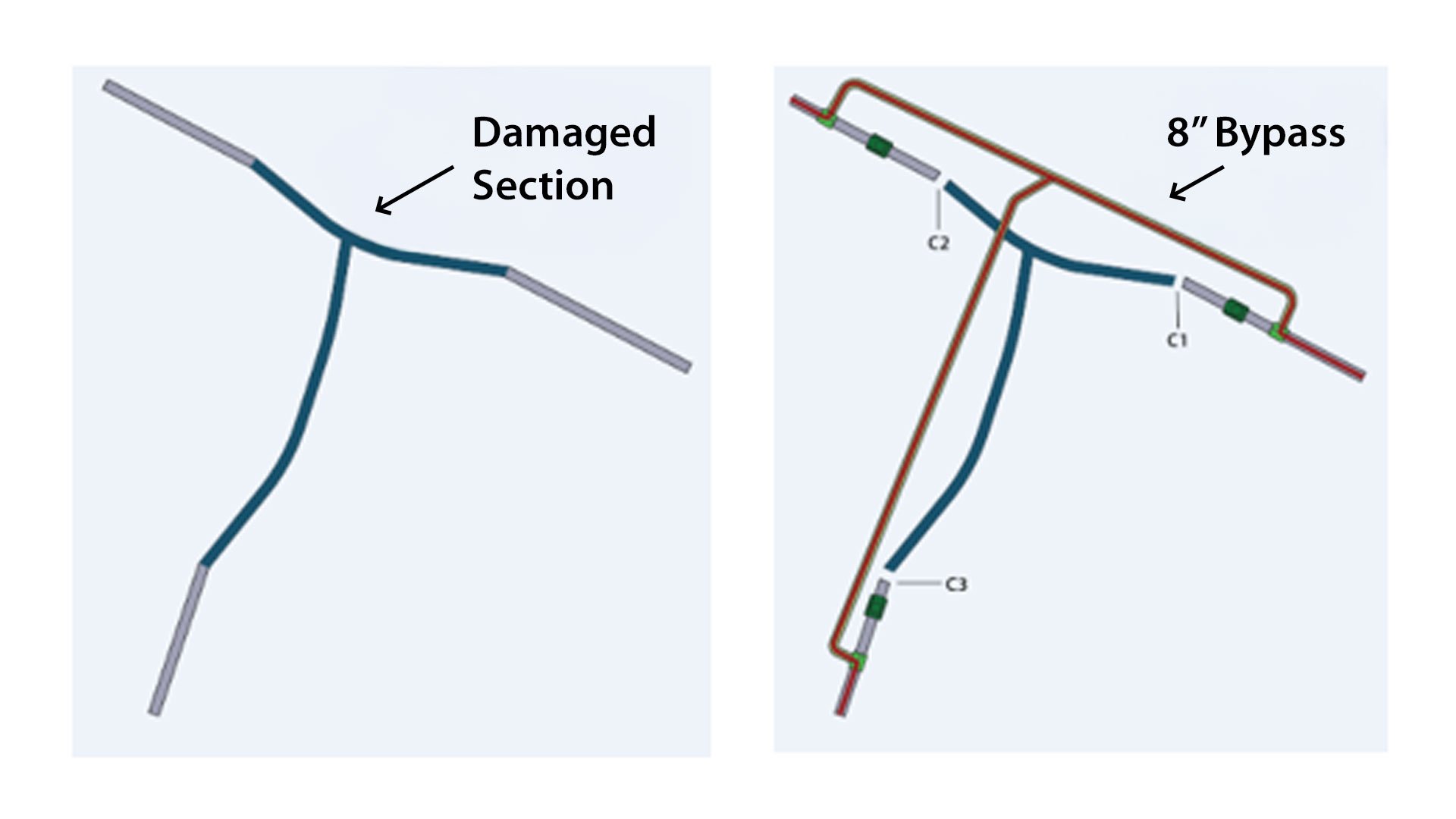
Original Pipeline Layout (left). Pipeline with Permanent Bypass (right).
Meeting the Challenge: Diver-Safe, Production-Focused Repair
STATS and CUEL worked together to develop an isolation and repair solution that would allow the damaged section of pipeline to be isolated and safely removed from the system, with no impact to production, the environment or risk to diver safety.
STATS’ patented BISEP tool was selected to provide leak-tight isolation of the pressurised pipeline. The BISEP is deployed through a full bore hot tap penetration at the isolation location through a mechanical hot tap clamp. The DNV type approved BISEP provides a fully proven, fail-safe, double block and bleed ( DBB) isolation barrier from the pressurised pipeline. This level of isolation complies with industry guidance on isolation and intervention for diver access to subsea systems, ensuring diver and worksite safety.
The pipeline repair solution incorporated the installation of a permanent bypass pipeline, which allowed the operations to be completed without the need for shutting-in pipeline production or depressurising, thus, ensuring production was maintained uninterrupted. Once the repair methodology was agreed and comprehensive risk assessment complete, STATS commenced key engineering and manufacturing operations to meet the project schedule.
Highlights
- A cost-effective solution to maintain uninterrupted production
- Commitment to safety in a high risk environment: prioritising diver safety.
- A versatile and integrated solution using STATS' Multi-Tool Technology
- Commitment to quality and operational integrity with rigorous testing, training and verification
- Complex subsea intervention expertise including hot tapping on a live pipeline, precision deployment of bypass spools and the use of saturation divers.
- Mitigating potential environmental impact by securely sealing the open ends for long-term wet storage.
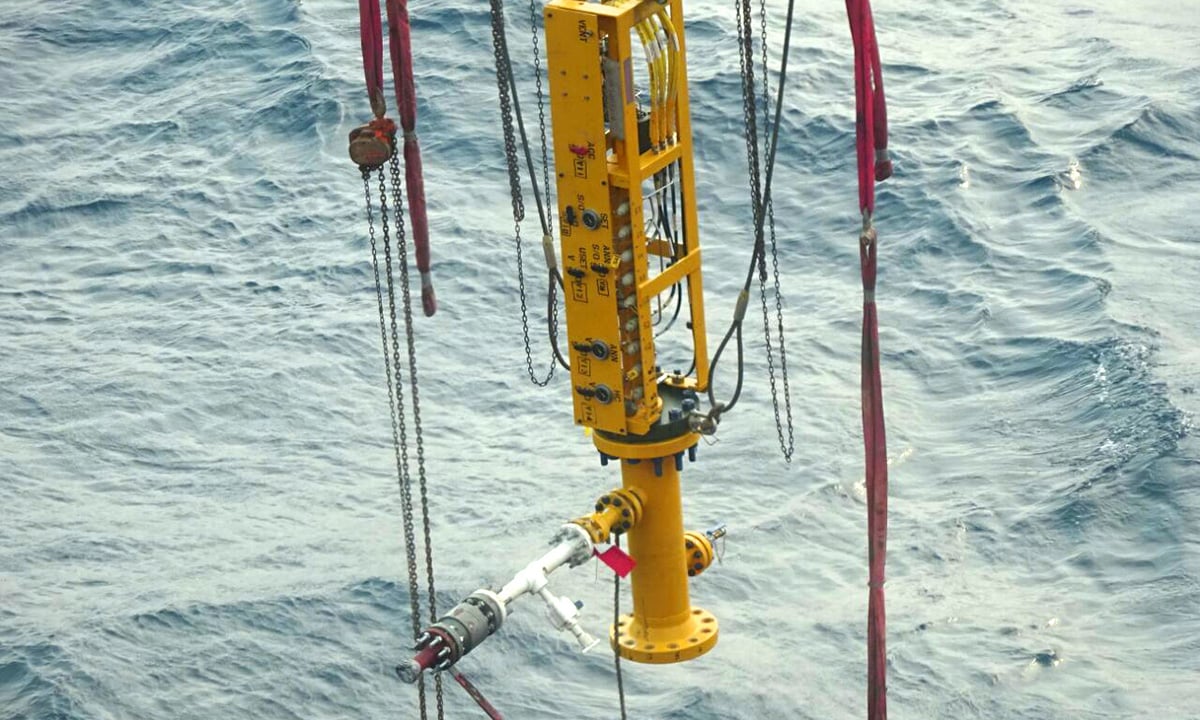
Integrated Testing and Training with Client and Dive Teams
Prior to deployment offshore, STATS shipped all the equipment to Thailand and performed a representative test scope that involved all the key stakeholders of the project, including the vessel dive team.
By following a dedicated training programme onshore in Thailand, the vessel dive team were fully trained in the use of the subsea hot tap machine and successfully carried out the six hot taps on the pipeline.
The testing scope used actual pipe sections and methodology that reflected the offshore operations with STATS’ technicians and client engineers.
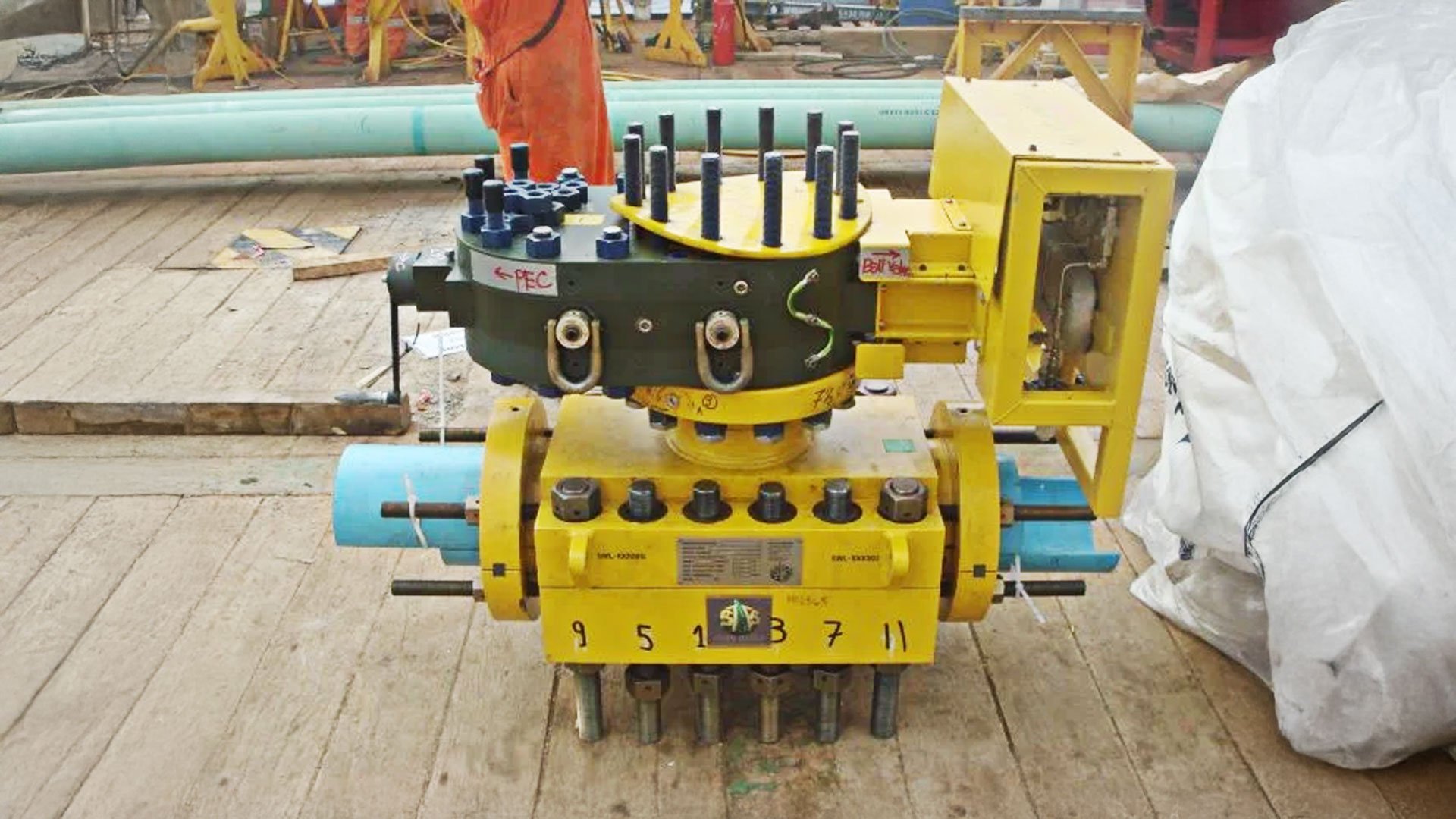
8" Hot Tap Clamp and Slab Valve
The subsea operations commenced with the excavation and concrete removal of the pipeline at key sections, to allow for the installation by divers of six permanent 8” mechanical hot tap clamps with 8” branched offtakes. At each of the three locations, a hot tap clamp was installed to provide a tie-in for the bypass pipeline and a second hot tap clamp as the entry point for the BISEP isolation.
During the offshore deployment, the subsea intervention stack-up was overboarded from the dynamic position diving support vessel ( DPDSV) and fitted to the pipeline by saturation divers. Once the hot tap clamps were installed and bolts tightened, a pressure test of the annulus and body flange was completed to verify the pressure integrity of the clamp to the pipeline at 56 bar. Key measurements were taken throughout by STATS’ technicians and, once the hot tap machine testing was completed, the hot tap machine cutter was then advanced to cut the hole in the pressurised pipe.
Once hot tapping was complete, the cutter was retracted, complete with the pipe coupon back through the valve and into the hot tap machine adaptor. The valve was then shut and pressure integrity tests were completed to allow the hot tap machine to be unbolted and recovered to the surface. Once the hot tap machine was recovered to the vessel deck, the coupon was removed, inspected and key dimensions verified.
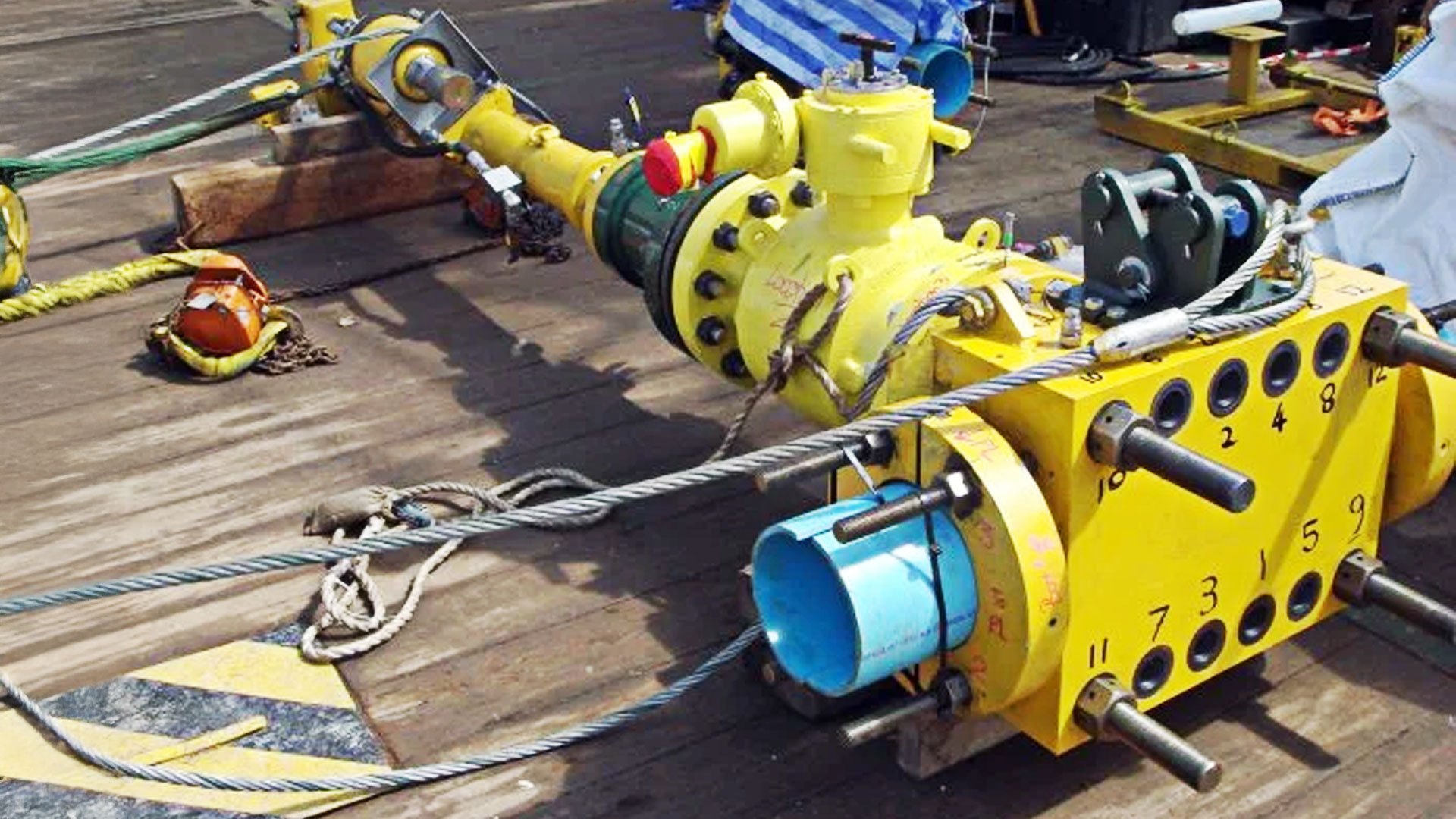
Hot Tap Machine and Clamp deployment
Establishing Flow, Ensuring Isolation: The Core of the Repair Strategy
On completion of the hot tapping work scope, the next stage of the operation was to fit the permanent subsea bypass spool. The bypass spool was fabricated in lengths and deployed from the vessel to the seabed for careful positioning by divers. The final tie-in spools were then connected, creating a bypass around the damaged pipe section. Once the flange joints were tested, the valves mounted to the STATS hot tap clamps were opened to allow flow from the pipeline into the bypass section, as well as the original pipeline.
The next phase of operations was to install the subsea BISEP’s at each of the three isolation locations. The BISEP’s were overboarded from the DPDSV and connected to the STATS supplied (DBB) subsea slab valves that were bolted to the hot tap clamps. Once the necessary integrity tests were completed, the BISEP was activated via a hydraulic umbilical on the vessel deck to a hydraulic control console. The BISEP head was then deployed into the pipeline, and the head compressed to activate the primary and secondary seals.
Once the BISEP head was deployed into the pipeline at each of the three isolation locations, the pipeline content was re-routed through the new 8” bypass, ensuring that production was always maintained. Each BISEP then completed a series of seal tests to verify full integrity of the primary and secondary seals to achieve a DBB isolation barrier of the pressurised pipeline. Upon completion of the BISEP seal testing, an isolation certificate was issued and renewed every 12 hrs.
From Isolation to Separation: Flushing And Cutting The Pipeline
With the damaged section of pipeline isolated, flushing of the pipeline product was then carried out. A 2” hose was deployed from the vessel and connected by divers to the 2” connection point on the BISEP launcher. A second 2” hose was then connected to another BISEP launcher and the other end tied into the subsea flushing port on the permanent spool. Using a water pump on the vessel deck, the gas condensate was flushed from the isolated damaged section back into the export pipeline.
Once flushing operations was completed, the damaged section was depressurised to the subsea ambient pressure of 6 bar. Divers could then be deployed to cut the pipeline. At each of the three identified cut locations, the coating was removed from the pipeline and diamond wire cutters were used to sever the pipeline. The damaged section of pipeline was then freed from the main pipeline and moved aside.
In order to provide a barrier to the marine environment for long term wet storage of the damaged pipe section, STATS supplied three 8” #150 subsea abandonment plugs, which were installed by the divers into the open pipe ends. The mechanically activated abandonment plugs incorporate a set of taper lock grips and a single seal.
Deploying Mechanical Connectors: A Secure & Tested Pipeline Termination
Once the damaged pipeline section was abandoned and capped, the bare ends of the original pipeline were left exposed. To provide a pressure competent termination, STATS supplied permanent subsea mechanical connectors complete with a blind flange that were fitted to the three bare pipe ends. The 8” #300 connectors were lowered from the vessel and installed to the pipeline by the divers. Once fitted over the end of the pipe, the bolts were torqued to compress the internal lock and seal mechanism, securely gripping the outside of the pipe.
STATS mechanical connectors provide permanent connection without swaging the pipeline. Upon installation, an annulus test of the cavity between the two internal seals of the connector was completed at 56 bar to confirm the connector integrity. A further internal test of the connector was completed via the body cavity by applying pressure through the BISEP launcher to pressurise the bore of the remaining pipe section.
This complex subsea pipeline repair project presented many operational and technical challenges. The successful completion demonstrates STATS ability to accommodate complex operations while maintaining high levels of safety at all times. STATS range of subsea isolation and intervention equipment provides operators a turnkey service for pipeline repair scenarios and establishes STATS capabilities within the subsea market. We will use the experience and our proven track record of first class delivery of these major projects to seek out other global opportunities for similar subsea contracts.

Gareth Campbell
Successful Installation
Following the successful installation and test of the subsea connectors, the BISEP was then hydraulically unset. The BISEP head was retracted back into the launcher and the slab valve closed. Following a purge of the BISEP launcher to remove any residual gas condensate, the valve was then subject to testing to ensure pressure integrity. The BISEP flange was then unbolted by the divers and the BISEP was removed and recovered to the surface.
On recovery of the BISEP, the hot tap machine was converted on the vessel deck to allow for the installation of STATS 8” #600 subsea completion plug. The hot tap machine was then redeployed subsea, complete with the completion plug and installed to the slab valve. Flange integrity tests were then completed before the slab valve was opened. The hot tap machine was then used to deploy the completion plug through the valve and into the flange of the hot tap clamp and secured in place by lock segments that are actuated by the diver. The completion plug was then subjected to pressure testing and monitoring to ensure pressure integrity from the pipeline. The hot tap machine – complete with the slab valve – was then removed from the hot tap clamp, leaving only the STATS completion plug installed. A blind flange was then installed by the diver to provide an additional barrier from the pipeline contents. The same procedure was then repeated at the two other locations, concluding a successful subsea isolation and repair operation.
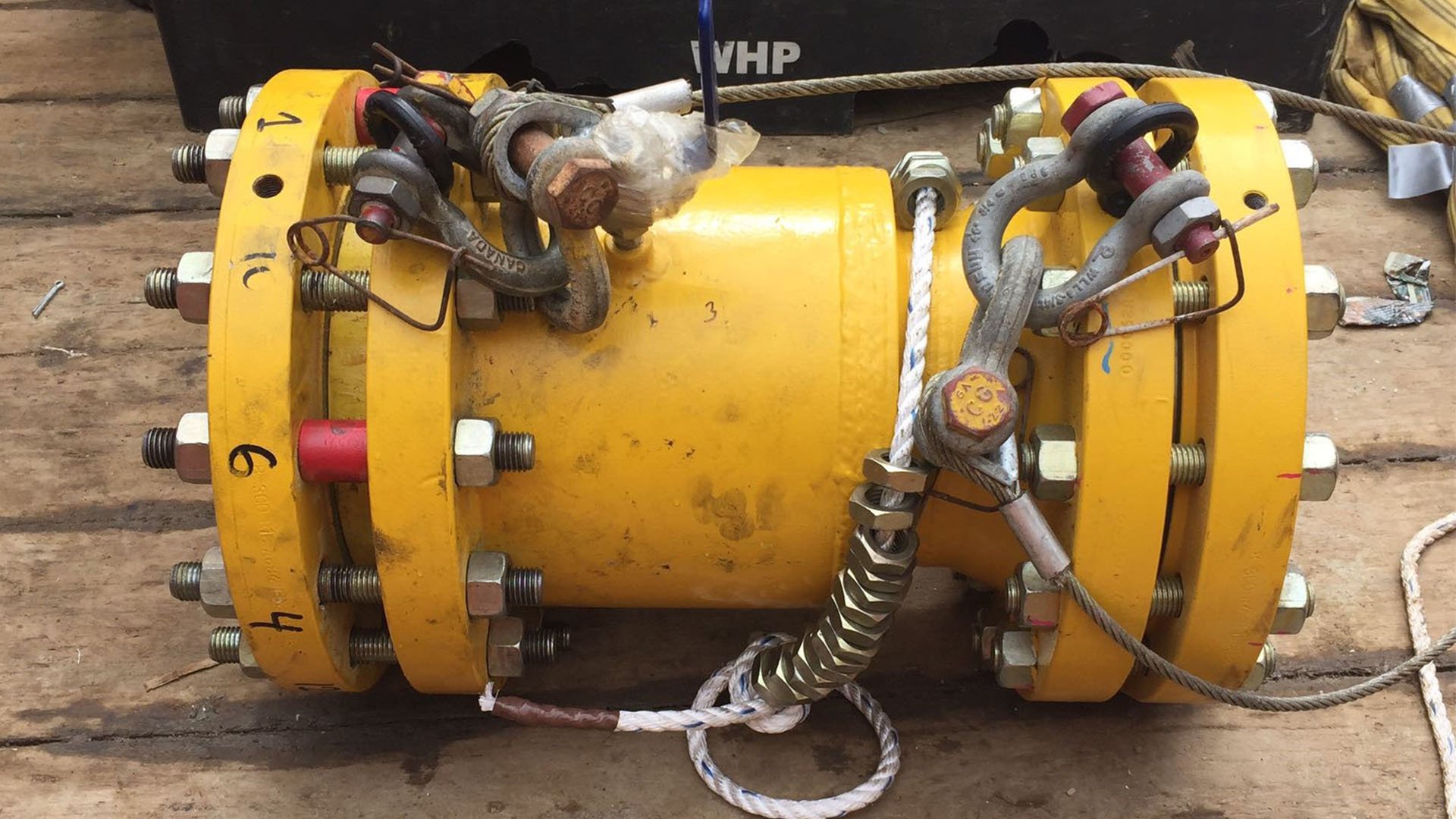
8" Subsea Mechanical Connector
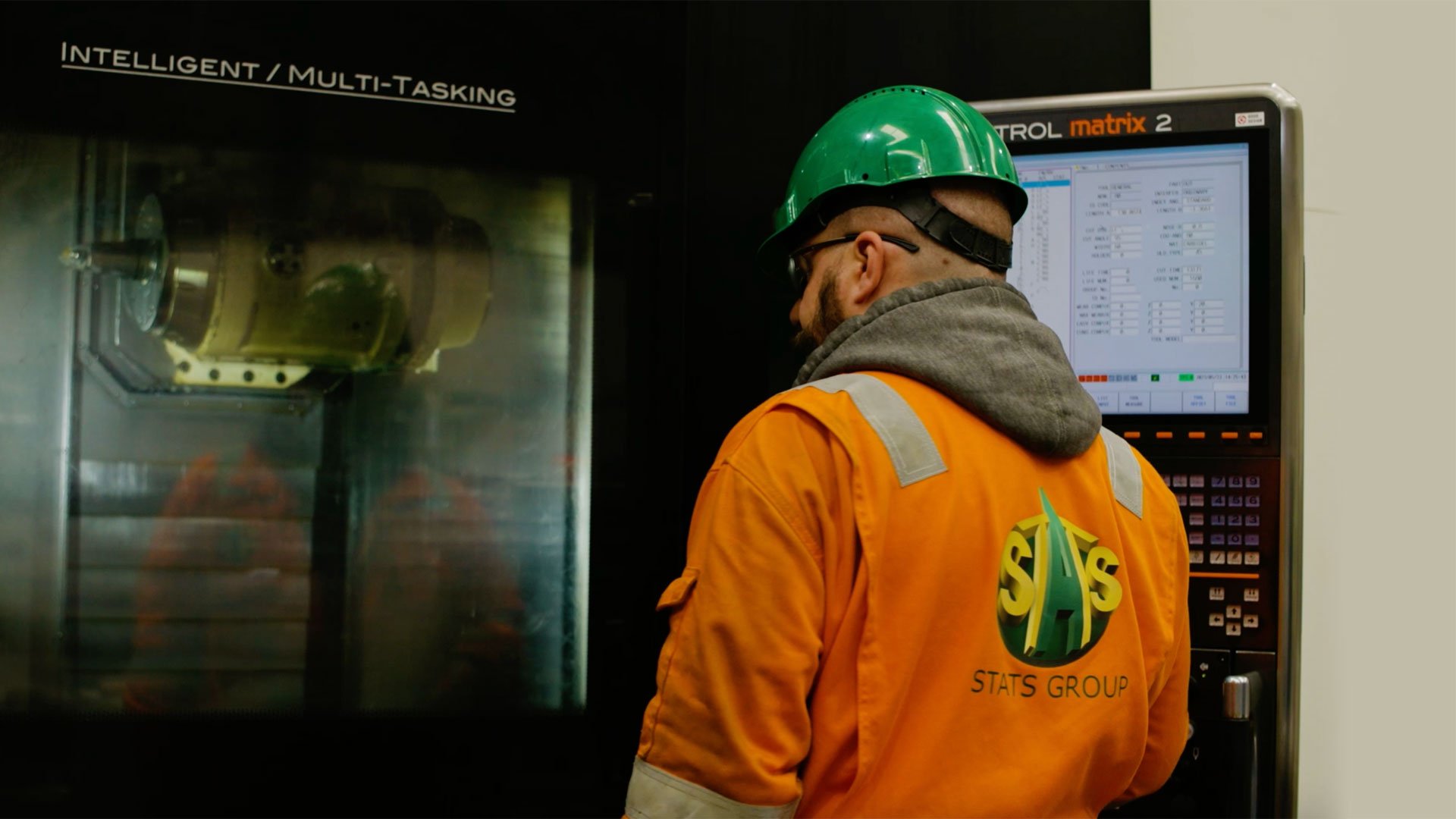