Case Study
Long Distance Deployment of 30" In-Line Weld Test Tool
Tool - In-line Weld Test Tool
Location - UK
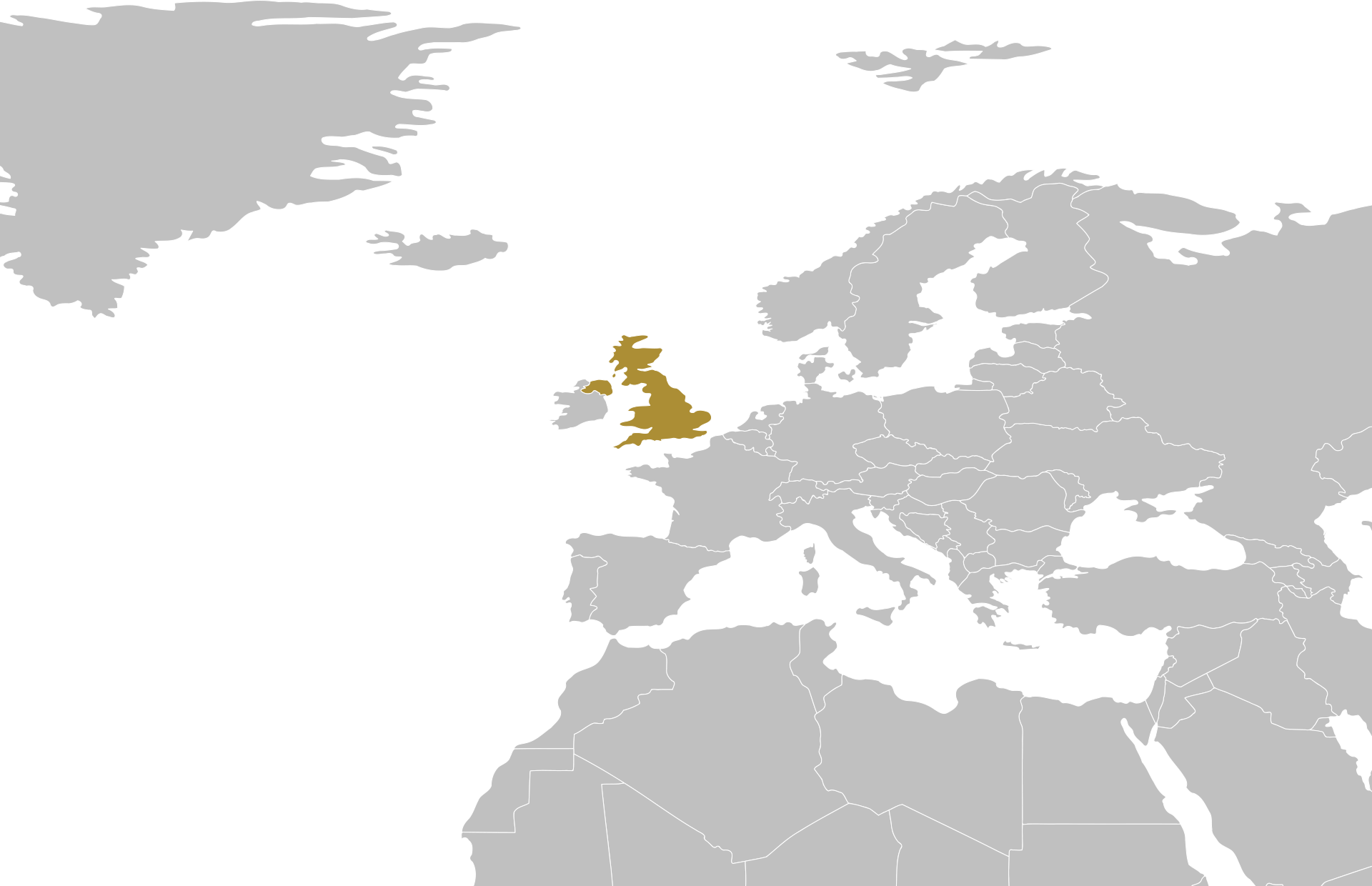
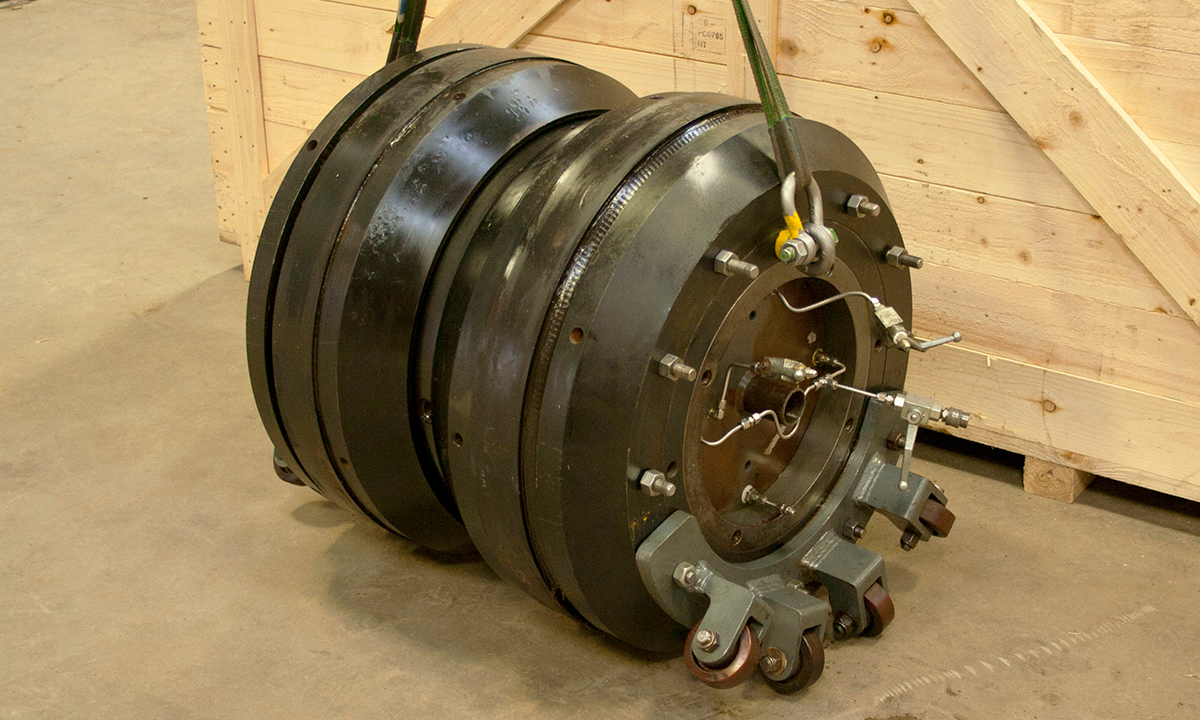
STATS Group has successfully completed the long-distance deployment of a 30" In-Line Weld Test Tool at a gas processing terminal in Scotland.
Typically, weld test tools are installed directly into an open-ended pipe so the challenge for this project was to successfully deploy the test tool 30 meters into the pipeline to the exact isolation and test location.
Based on the initial enquiry from a multinational engineering and consulting company, STATS were requested to support a critical pipeline isolation and testing operation, with the test tool being installed into the open pipe end. However, as the project progressed the client changed the scope of work based on discussions with the STATS team to deploy the In-Line Weld Test Tool from the pig launcher on a tether to the isolation and test location, marking a first for STATS Group at this pipeline size and distance.
To ensure first time success and exact positioning of the test tool at the location an engineering assessment was conducted to design a long-distance deployment aid and provide the client with a detailed methodology to support client understanding and gain approval.
Prior to mobilisation to site STATS performed a successful Factory Acceptance Test (FAT) witnessed by the client.
Inline weld test tools are designed to improve shutdown efficiency, the dual use of the tool allows it to be deployed prior to hotwork as a verified vapour barrier, greatly increasing worksite safety. Inline test tools feature a thru port to safely monitor the downstream to ensure no pressure build-up. The client required a verified vapour barrier in place during all spool replacement operations, so STATS had to devise a method to deploy and hydraulically set the test tool at location, disconnect the hydraulic control lines to remove and replace the spool and later reconnect the lines without compromising the isolation barrier.
Once the spools were replaced and welded into position, the inline weld test tool was unset and repositioned to conduct a hydrostatic test of the new weld at 260 bar.
The use of localised weld testers to verify the integrity of new welds significantly reduces the volume of water required to perform a test, preventing the pipeline from being flooded and then dewatered, significantly reducing the volume of contaminated water to be treated and disposed of, limiting environmental impact.
Our extensive track record of supporting shutdowns and turnarounds provides us with the knowledge to support clients with unique challenges to engineer a solution to ensure the project can be delivered efficiently and safely, minimising shutdown time. As our tools are hydraulically activated, they provide significant safety benefits, avoiding torquing and untorquing tool activation bolts, removing personnel from high risk areas. Large elastomer seals can be energised in a controlled manner and to exact pressures increasing safety and project efficiency.

Stuart Rae
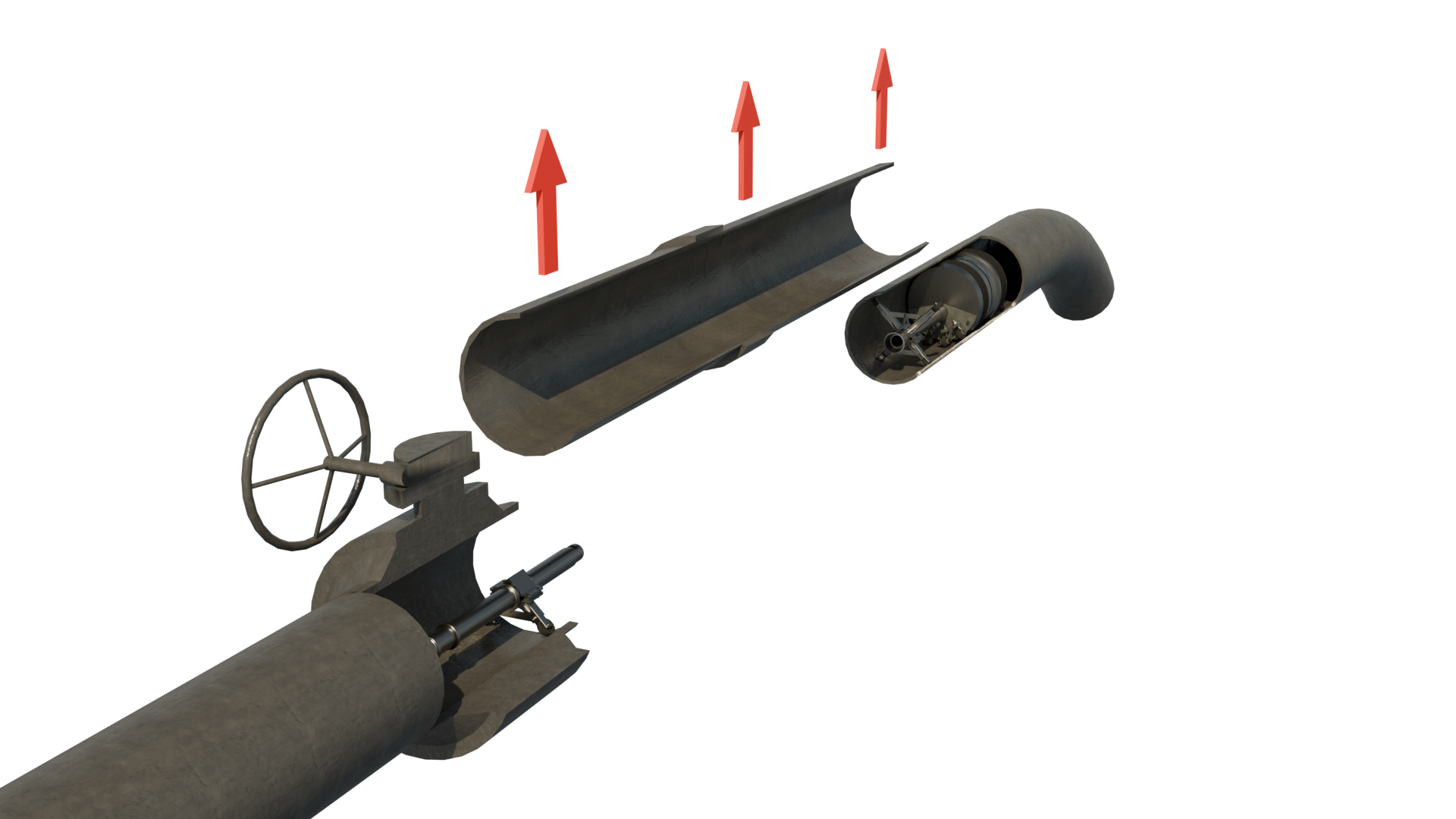
In addition to supporting the project, STATS supplied Flanged Weld Test Tools to allow additional hydrostatic tests to be carried out on the pipeline at the same time. The result was a successful, efficient and innovative execution that reduced downtime and delivered significant operational value to the client.
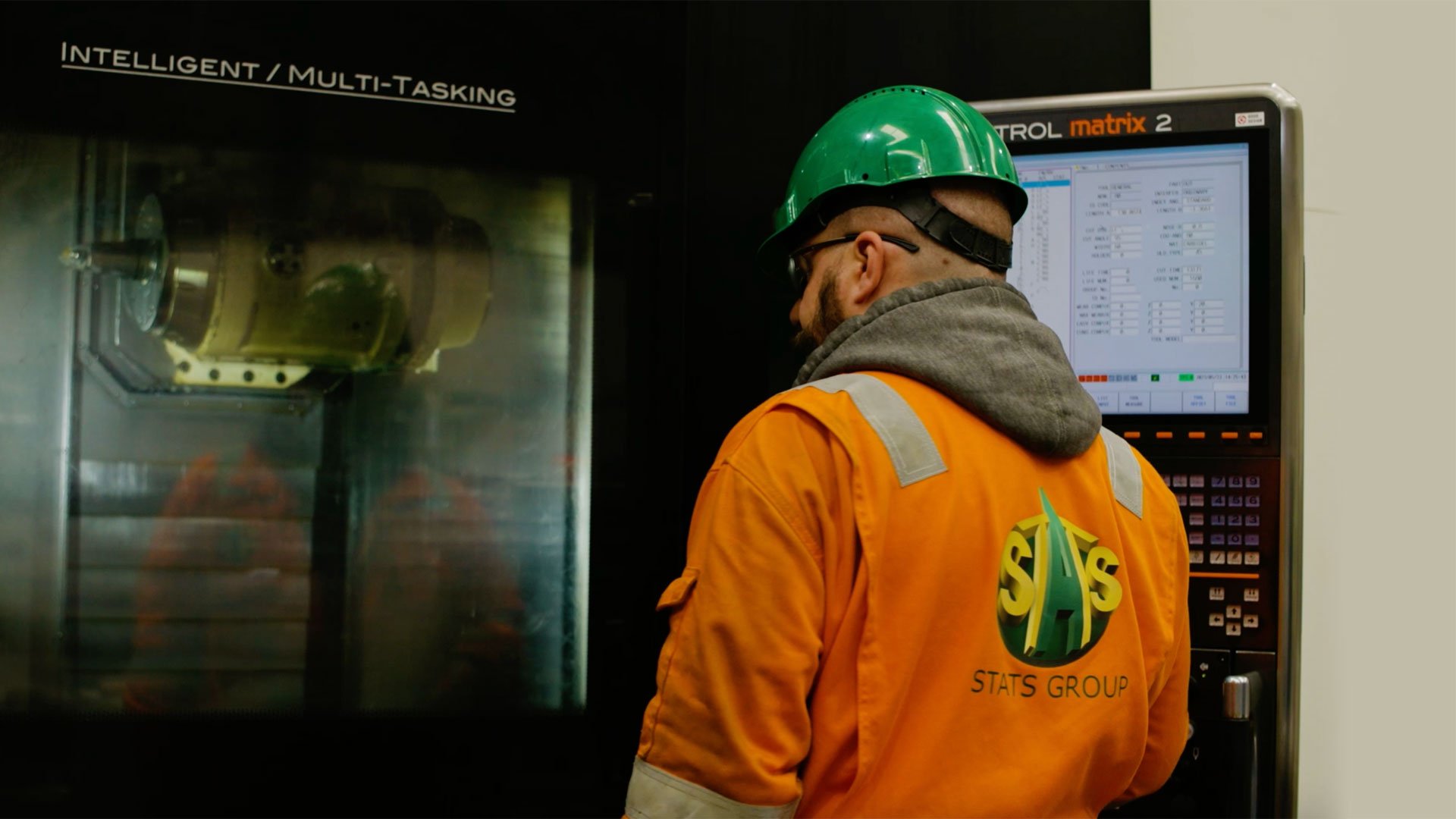