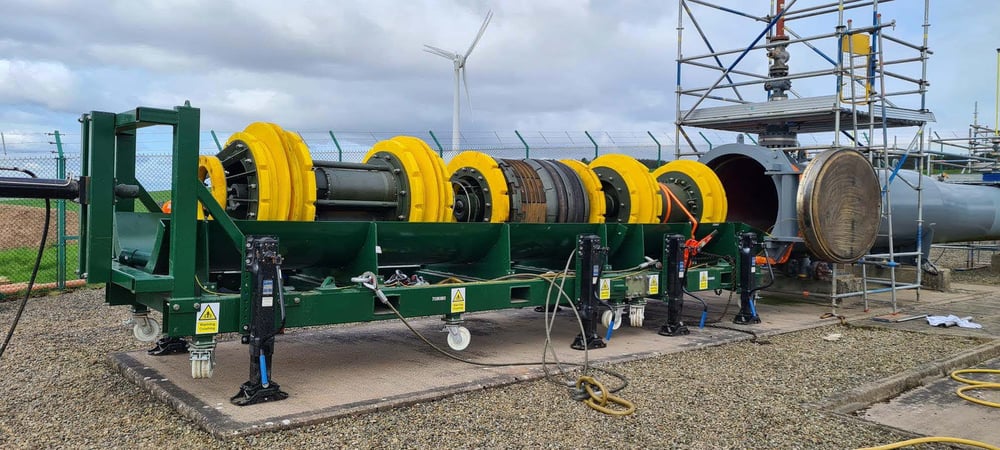
A real-world example is discussed where a double block inline isolation tool facilitated pipeline modification, resulting in reduced project costs and production downtime, while significantly minimising the discharge of emissions.
Abstract
Operators can often encounter difficulties in isolating sections of their pipeline to facilitate essential safe repair or maintenance activities. Inline isolation pigs provide fully proven and monitored dual seal barriers that ensure the safe breaking of containment on pressurised systems in compliance with the highest industry standards.
Inline isolation tools significantly reduce, and in some cases eliminate, the requirement to vent or flare harmful emissions into the atmosphere during maintenance activities. One of the most significant environmental advantages is the substantial reduction in greenhouse gas emissions verses venting the pipeline. In the case of long, large diameter gas pipelines, this can prevent the potential discharge of thousands of tons of greenhouse gases into the atmosphere.
Following the completion of maintenance activities, a reinstatement leak-test of the replaced valve or pipework can be performed while the isolation is still in place, providing an alternative to golden welds.
A real-world example is discussed where a double block inline isolation tool facilitated pipeline modification, resulting in reduced project costs and production downtime, while significantly minimising the discharge of emissions.
The utilisation of inline isolation tools not only enhances the efficiency and safety of pipeline repair and maintenance but also aligns with increasing demand to reduce emissions and create a more sustainable energy infrastructure for the future.
Author: Neil Mackay BEng CEng IMechE